At Precision Machining Pro, we understand the importance of cost-effective manufacturing solutions. CNC machining is a widely used method for producing precision parts, but it’s crucial to consider the various factors that can influence the price of CNC machining services. By gaining insights into these factors and staying informed about recent industry trends, businesses can optimize their manufacturing budget and find the best price for CNC machining without compromising on quality.
With our expertise in CNC machining and our commitment to delivering affordable and high-quality machining services, we aim to help businesses make informed decisions and achieve their machining goals. In this article, we will explore the key influences on CNC machining prices and discuss recent trends in the industry. By understanding CNC machining price factors and trends, businesses can ensure they receive cost-efficient and reliable machining services that meet their requirements.
Key Takeaways:
- Several factors can impact the price of CNC machining services, including quantity, design features, materials, tolerances, thickness, size, precision, setup time, production volume, machining time, skilled labor, machine types, and additional costs.
- Optimizing CNC machining costs involves balancing these factors and making informed decisions about material selection, design complexity, production volume, machining time, skilled labor utilization, and machine types.
- Understanding market trends and economic factors is essential for adapting to changes in the CNC machining industry and ensuring long-term success.
- By considering the key influences on CNC machining price and staying abreast of industry trends, businesses can negotiate the best price for their CNC machining projects and achieve cost-effective and high-quality results.
- At Precision Machining Pro, we are dedicated to providing affordable CNC machining solutions that meet the highest standards of precision and quality.
The 7 important CNC machining price factors to get your best price
When it comes to determining the price of CNC machining, there are several important factors to consider. These factors can greatly impact the final cost of your machining project and play a crucial role in finding the best price for your CNC machining needs. By understanding these factors and their influence on pricing, you can make informed decisions and ensure that you receive cost-effective and high-quality machining services.
Quantity for pricing
The quantity of parts being produced is a significant factor in CNC machining pricing. As the volume of parts increases, economies of scale come into play, making each part less expensive. This is because fixed charges like setup and tooling costs can be spread over a larger number of units. Quantity pricing is particularly beneficial for businesses that require large production runs, as it can significantly reduce the price per part.
Design features for pricing
The design features of your parts can also impact the price of CNC machining. Intricate or complex designs often require more advanced machinery, skilled operators, and longer machining times, all of which contribute to higher costs. However, these designs can also result in higher precision and better product performance. Balancing design complexity, precision requirements, and production time is essential to optimize pricing without compromising quality.
Materials that impact price
The choice of materials used in CNC machining can have a significant impact on the price. High-performance materials like titanium or stainless steel are generally more expensive than plastics or softer metals. Factors like material properties, machinability, and market pricing will influence the overall material costs. It is important to balance material attributes with cost-effectiveness to ensure optimal performance and economic feasibility.
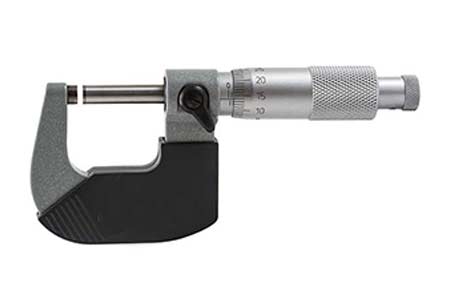
Tolerances required can impact pricing
The tolerances required for your parts can influence the price of CNC machining. Tighter tolerances often require more precise machining processes and closer monitoring, which can increase costs. It is important to accurately define the tolerances required for your parts and communicate them effectively with your CNC machining service provider to ensure accurate pricing.
Thickness of parts considerations for pricing
The thickness of your parts can also impact CNC machining pricing. Thicker parts may require more material and longer machining times, resulting in higher costs. Understanding the relationship between part thickness and machining complexity is crucial for accurate pricing.
The size of the parts affects on pricing
The size of your parts can affect CNC machining pricing. Larger parts may require larger machining equipment and more complex setups, which can increase costs. It is important to consider the size of your parts and its impact on machining requirements to ensure accurate pricing.
The Impact of Precision and Speed on Reducing Time to Market
Precision and speed play a significant role in CNC machining pricing. Higher precision requirements and shorter lead times often require more advanced equipment and skilled operators, which can increase costs. However, by investing in precision and reducing time to market, businesses can gain a competitive edge and achieve faster product launches. It is important to balance precision and time-to-market considerations to optimize CNC machining pricing.
By considering these seven important factors – quantity, design features, materials, tolerances, thickness, size, precision, and time to market – businesses can negotiate the best price for their CNC machining projects. Understanding these factors empowers you to make informed decisions and ensure your machining needs are met with cost-effective and high-quality solutions.
Material Costs: The Foundation of CNC Machining Price
One of the key factors that impact the price of CNC machining is the cost of materials. The type of material used for machining projects can vary significantly in price, with high-performance materials such as titanium or stainless steel being more expensive than plastics or softer metals. The properties of the material, its machinability, and the current market pricing all influence the overall material costs for CNC machining. Additionally, certain materials may require post-processing to achieve desired finishes, which can also add to the expense.
Balancing material attributes with cost efficiency is essential in CNC machining to ensure both optimal performance and economic feasibility. By carefully selecting materials, businesses can achieve the best price for their projects without compromising on quality. Understanding the impact of material costs is crucial for making informed decisions and optimizing CNC machining expenses.
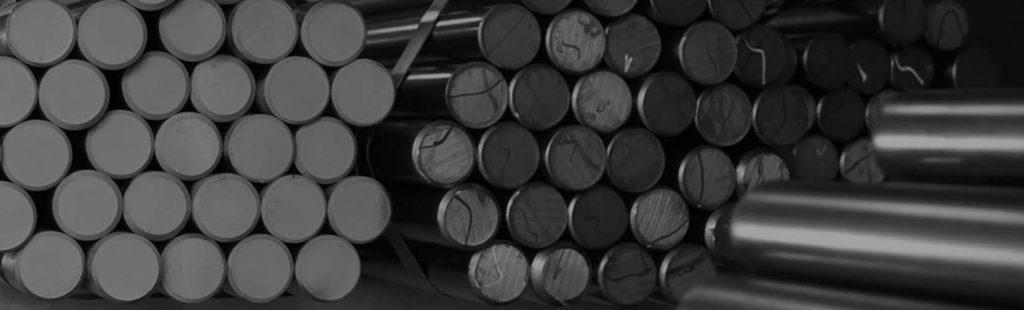
Complexity and Cost: How Design Affects CNC Machining Price
The complexity of the design is a crucial factor that can have a significant impact on the price of CNC machining. Intricate designs often require advanced machinery, skilled operators, and extended machining times, all of which contribute to higher costs. Achieving tight tolerances and intricate features in a design may necessitate the use of specialized tools and methods, further increasing expenses.
However, it is important to consider the trade-offs associated with design complexity. While complex designs can drive up costs, they can also result in higher precision and better product performance. Finding the right balance between design complexity, precision requirements, and production time is essential in determining the optimal design for a given budget.
The Challenge of Intricate Designs in CNC Machining
Intricate designs pose unique challenges in CNC machining. The intricate features and tight tolerances require precise tool paths and careful attention to detail during the machining process. Skilled operators and advanced machinery are necessary to ensure the accuracy and quality of the final product.
Additionally, the production time for intricate designs is often longer compared to simpler designs. The complex geometry and fine details require more machining passes and potential manual interventions, resulting in increased labor and machine costs.
Overcoming these challenges requires advanced planning and collaboration between designers, engineers, and CNC machining experts to optimize the design for manufacturability without compromising on functionality or quality.
Evaluating the Trade-offs Between Precision and Production Time
Design decisions can have a significant impact on both precision and production time in CNC machining. Higher precision requirements, such as tighter tolerances or complex geometries, may increase machining time as more accurate tool paths and multiple machining passes are needed to achieve the desired precision.
Conversely, reducing precision requirements or simplifying the design can help optimize production time and reduce costs. However, this may come at the expense of sacrificing certain intricate features or compromising on the overall performance of the part or product.
It is essential to carefully evaluate the trade-offs between precision and production time to strike the right balance between cost, functionality, and performance. Collaborating with experienced CNC machining professionals and leveraging their expertise can help identify the optimal design approach that meets the required precision while minimizing production time and costs.
Design Aspect | Impact on Price |
---|---|
Intricate geometry and tight tolerances | Higher machine and labor costs |
Complex tool paths and multiple machining passes | Increased production time and labor costs |
Specialized tools and methods | Additional expenses |
Precision requirements | Potential increase in machining time and costs |
Simplified design and reduced precision | Potential trade-off between cost and functionality |
Note: The table above illustrates the potential cost implications of various design aspects in complex CNC machining designs.
Production Volume: Scaling Costs in CNC Machining Operations
The volume of production plays a crucial role in determining the costs of CNC machining operations. As production volumes increase, economies of scale come into play, resulting in reduced costs per part. This cost reduction occurs because the fixed charges, such as setup and tooling costs, are spread over a larger number of units. The optimization of production volume is essential to achieve cost-efficient CNC machining.
In large-volume production, the per-part expense for setup is significantly lower, leading to lower overall costs. This is because the setup costs are distributed across numerous parts, reducing the individual cost burden. On the other hand, smaller production batches result in higher setup costs per component, increasing the price per unit. Striking the right balance between volume and setup efficiency is critical for optimizing CNC machining costs.
To illustrate this concept, let’s consider an example. Precision Machining Pro, a leading CNC machining service provider (http://precisionmachiningpro.com), received an order for 1,000 parts. The setup time for this order accounted for a relatively smaller portion of the total machining time, resulting in a lower cost per part. However, if the same order were divided into smaller production batches of 100 units each, the setup time would represent a more significant portion of the total machining time, driving up the price per component.
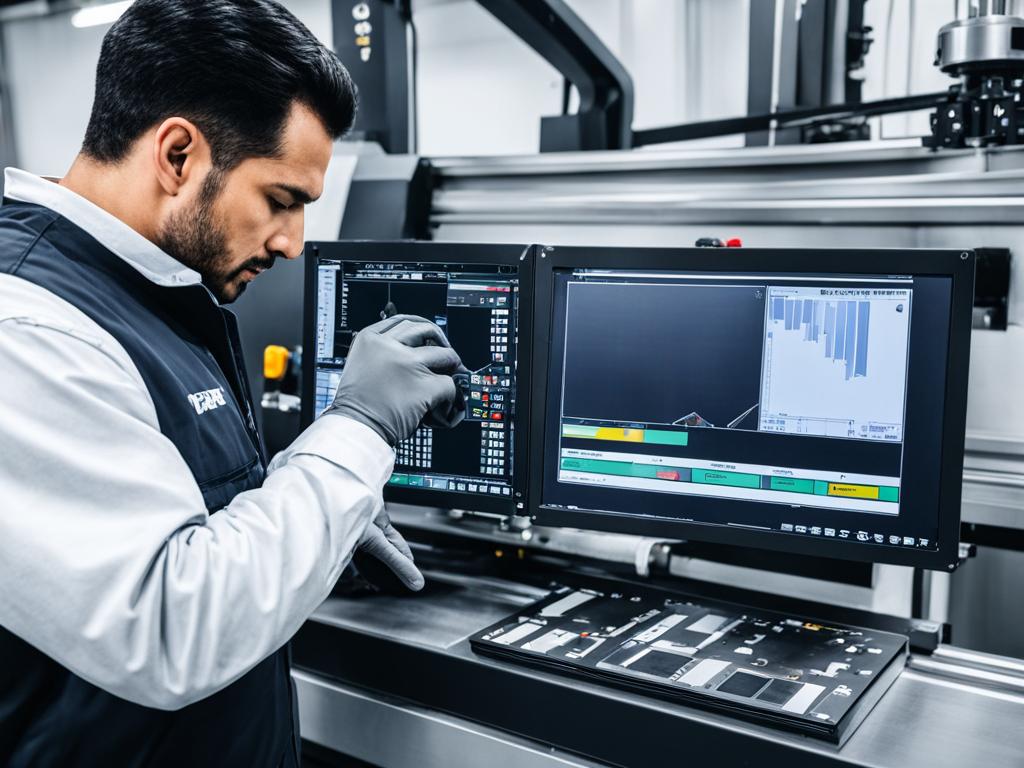
To ensure cost-efficient machining operations, it is essential to analyze the optimal production volume that strikes a balance between volume and setup efficiency. By carefully considering the production requirements, businesses can determine the most cost-effective batch sizes and minimize expenses.
Moreover, achieving the optimal production volume requires a thorough assessment of the specific project’s requirements. Factors such as demand forecasts, product lifecycle, market conditions, and budget constraints should be taken into consideration when determining the ideal production volume.
By finding the right balance between production volume and setup efficiency, businesses can maximize the cost-efficiency of their CNC machining operations while maintaining high-quality standards. This strategic approach leads to improved profitability and competitive advantages in the market.
Timelines and Techniques: The Impact of Machining Time on CNC Pricing
The time it takes to machine a part has a direct impact on the cost of CNC machining. This includes both the actual cutting or cycle time and the setup time, which involves tool changes and preparation. The longer it takes to machine a part, the higher the cost. Therefore, it is essential to optimize machining time to achieve cost-effective CNC machining.
Setup Time and Its Effect on Cost
Setup time is a critical factor that influences CNC machining costs. It encompasses the activities required to prepare the CNC machine for machining a specific part, such as changing tools, setting up workholding, and configuring machine parameters. The more complex the part or design, the longer the setup time typically takes, resulting in increased costs.
Reducing setup time is crucial for cost-effective CNC machining. By streamlining setup processes, implementing efficient tool change strategies, and utilizing advanced software for machine programming, businesses can minimize the time and resources required for setup, ultimately reducing machining costs.
Finding Efficiency in CNC Machine Cycle Times
In addition to setup time, the actual machine cycle time significantly impacts CNC pricing. Cycle time refers to the time it takes for the CNC machine to complete one full cycle of cutting a part. Factors such as the complexity of the design, the number of operations required, and the intricacy of the features can all contribute to longer cycle times and higher costs.
Efficiency in CNC machine cycle times is essential for cost-effective machining. By optimizing tool paths, utilizing high-speed machining techniques, and leveraging advanced CNC programming capabilities, businesses can reduce cycle times and enhance productivity, leading to lower machining costs.
It is also essential to consider the impact of precision and speed on reducing time to market. By achieving the required precision while minimizing cycle times, businesses can enhance their competitive advantage by delivering products to the market faster, resulting in increased customer satisfaction and potential cost savings.
To illustrate the impact of machining time on CNC pricing, we have provided a visual representation below:
As demonstrated in the image above, reducing machining time through efficient setup and optimized cycle times directly translates to cost savings. By prioritizing strategies that minimize machining time without compromising quality, businesses can achieve cost-effective CNC machining solutions.
Skilled Labor: Evaluating Its Influence on CNC Machining Costs
Skilled labor is a significant factor that influences CNC machining costs. At Precision Machining Pro, we understand the value of proficient operators who are knowledgeable in CNC setup, programming, and operation. Their expertise is essential for accurate and productive machining, ensuring high-quality results for our clients.
The cost of skilled labor contributes to the overall CNC machining expenses. However, effective utilization of skilled labor is crucial for striking a balance between budget control and leveraging their expertise. By optimizing the utilization of skilled labor, we can achieve cost-efficient CNC machining services without compromising on quality or precision.
We prioritize the training and development of our team to ensure they possess the necessary skills and expertise to handle complex CNC machining projects. Our skilled operators are equipped with the knowledge and experience to efficiently utilize CNC machines, resulting in improved productivity and reduced machining costs.
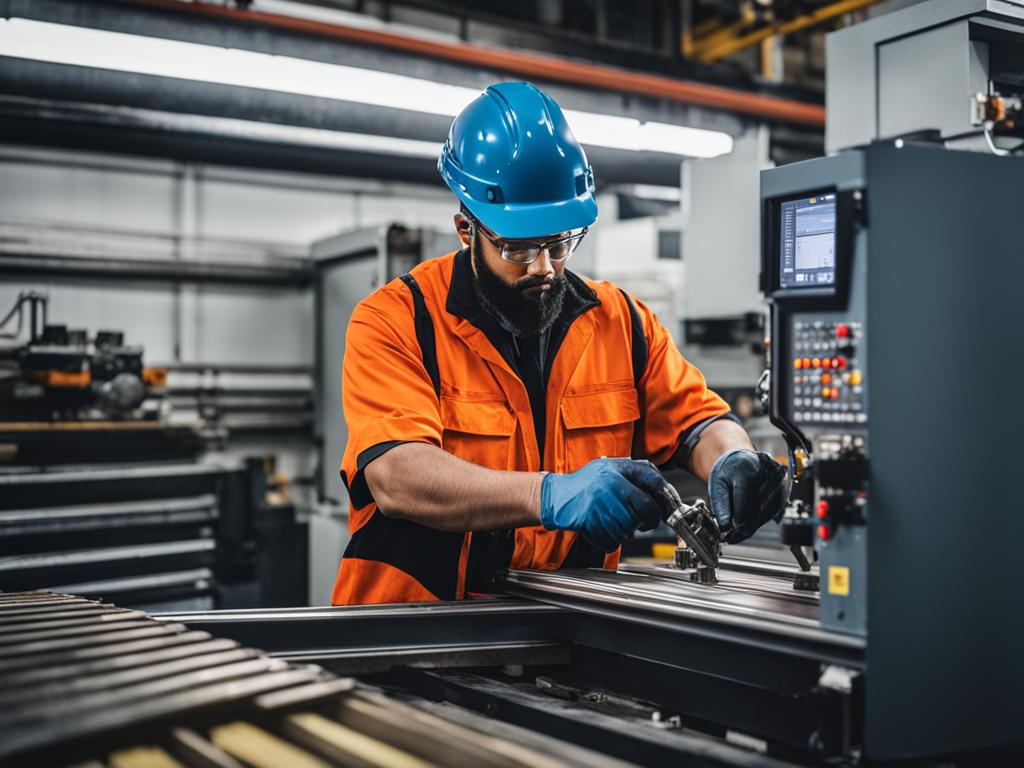
“Skilled operators who are knowledgeable in CNC setup, programming, and operation are essential for accurate and productive machining.”
By effectively utilizing skilled labor, we can optimize the CNC machining process, reduce setup time, and streamline production. Our skilled operators can identify opportunities for process improvements, implement effective strategies, and maximize the efficiency of our CNC machines. This not only helps to control labor costs but also ensures that our clients receive high-quality parts at competitive prices.
At Precision Machining Pro, we recognize the importance of skilled labor in CNC machining. We invest in our team, provide ongoing training, and strive for continuous improvement to optimize our manufacturing processes and deliver cost-effective machining solutions for our clients.
Assessing the Impact of CNC Machine Types and Costs
The type of CNC machine used in machining operations can have a significant impact on costs. Different types of CNC machines, such as CNC milling machines, CNC lathes, CNC routers, and CNC plasma cutters, have varying price ranges and capabilities. Understanding the price range of diverse CNC machinery is essential for accurately estimating CNC machining costs.
Calculating costs involves considering machine pricing and yearly usage rates. The upfront cost of a CNC machine and its expected yearly usage hours play a role in determining the machine shop rates, commonly known as machining charge per hour.
In this section, we will assess the impact of CNC machine types and costs on CNC machining prices, explore the price range of diverse CNC machinery, and discuss the calculation of CNC machine costs based on yearly usage rates.
Scrutinizing Additional Costs in the CNC Machining Process
In addition to the factors discussed in previous sections, there may be additional costs associated with the CNC machining process. These costs can include machine tool costs, surface finish costs, and specialized tooling costs, among others. Scrutinizing these additional costs is crucial for managing expenses and ensuring cost-effective CNC machining.
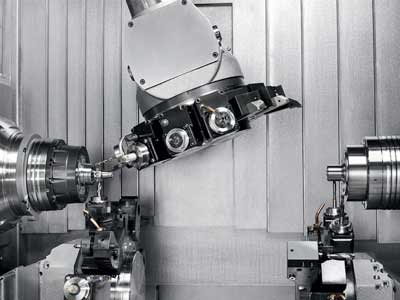
In order to manage and minimize additional costs in CNC machining, businesses should consider the following strategies:
- 1. Conduct a comprehensive cost analysis: It is important to thoroughly analyze all potential additional costs that may arise during the CNC machining process. This includes identifying any hidden costs that may not be immediately apparent.
- 2. Develop a detailed cost estimation system: By implementing a robust cost estimation system, businesses can accurately predict and budget for additional costs in the CNC machining process. This can help prevent unwanted surprises and ensure cost control.
- 3. Explore alternative suppliers and vendors: Comparing prices, quality, and services offered by different suppliers and vendors can help businesses find the most cost-effective options for machine tool purchases, surface finishes, and specialized tooling.
- 4. Optimize production processes: Streamlining production processes and reducing waste can help minimize additional costs in CNC machining. This can be achieved by implementing lean manufacturing principles and continuous process improvement strategies.
- 5. Invest in preventive maintenance: Regular maintenance of CNC machines can help prevent unexpected breakdowns and costly repairs. By investing in preventive maintenance, businesses can avoid downtime and additional expenses.
By scrutinizing and managing additional costs in the CNC machining process, businesses can achieve greater cost efficiency and improve their bottom line. It is essential to carefully analyze and consider all cost factors to ensure successful and financially viable machining operations.
Exploring CNC Machining Market Trends and Economic Factors
The CNC machining industry is constantly evolving, driven by various market trends and economic factors. Staying ahead of these trends and understanding the economic landscape is essential for businesses in the CNC machining market. By keeping abreast of industry dynamics and adapting to technological advancements, businesses can position themselves for success in this competitive field.
The Growth Trajectory of CNC Machine Market
The CNC machine market has experienced significant growth in recent years and shows no signs of slowing down. Technological advancements, increasing automation, and the demand for precision machining have been the key drivers of this growth trajectory. As industries such as aerospace, automotive, and medical continue to rely on CNC machining for high-quality parts, the market is expected to expand further.
“The market for CNC machines is projected to reach a value of $128.86 billion by 2027, growing at a CAGR of 7.0% during the forecast period.”
Source: Precision Machining Pro
The growth trajectory presents both opportunities and challenges for businesses operating in the CNC machining industry. As the market expands, competition intensifies, making it crucial for businesses to differentiate themselves by offering exceptional quality, cost-effective solutions, and efficient turnaround times.
Adapting to Automation and Robotic Integration in CNC Operations
Automation and robotic integration have revolutionized CNC operations, driving efficiency, accuracy, and productivity. Businesses that have embraced automation and integrated robotics into their CNC machining processes have gained a competitive edge. Automation reduces labor costs, minimizes errors, and allows for expanded capabilities in machining complex parts.
The integration of robotics in CNC operations streamlines workflows and enables lights-out manufacturing, where machining processes can run continuously without human intervention. This level of automation improves production efficiency and reduces lead times, allowing businesses to meet tight deadlines and fulfill customer demands effectively.
However, adapting to automation and robotic integration requires businesses to invest in advanced machinery, update their programming capabilities, and train their workforce. By embracing new technologies and reimagining their CNC operations, businesses can stay competitive and capitalize on the benefits of automation.
Adapting to Technological Advancements in CNC Machining
The CNC machining industry continues to witness rapid technological advancements that enhance efficiency, accuracy, and versatility. Advanced software systems, simulation tools, and real-time monitoring enable businesses to optimize their CNC operations and achieve higher levels of productivity.
Software advancements, such as computer-aided design (CAD) and computer-aided manufacturing (CAM) systems, simplify the design-to-production process, reducing lead times and enhancing precision. These tools enable businesses to create complex designs and simulate machining processes to ensure optimal results.
Real-time monitoring systems provide valuable data on machine performance, material utilization, and quality control, allowing businesses to make data-driven decisions and optimize their processes. By leveraging these technological advancements, businesses can improve their competitiveness, enhance customer satisfaction, and achieve cost-efficient CNC machining operations.
In the rapidly evolving CNC machining market, staying informed about market trends and economic factors is crucial. Understanding the growth trajectory of the CNC machine market, embracing automation and robotic integration, and adapting to technological advancements are key strategies for businesses seeking success in the CNC machining industry. By continuously improving their operations, leveraging advances in technology, and offering innovative solutions, businesses can thrive in this dynamic market.
Conclusion
In conclusion, understanding the factors that influence CNC machining prices is essential for businesses looking to optimize their manufacturing budget and find cost-efficient solutions. By considering factors such as quantity, design features, materials, tolerances, thickness, size, precision, setup time, production volume, machining time, skilled labor, machine types, and additional costs, businesses can negotiate the best price for their CNC machining projects. Staying abreast of market trends and economic factors is also crucial for adapting to changes in the CNC machining industry and ensuring long-term success. By utilizing the insights and strategies discussed in this article, businesses can achieve cost-effective and high-quality CNC machining services.
At Precision Machining Pro, we understand the importance of optimizing CNC machining costs without compromising on quality. Our team of experts is well-versed in the various factors that affect CNC machining prices, and we are committed to providing cost-efficient solutions for our clients. Through careful consideration of quantity, design features, materials, and other essential factors, we strive to deliver the best price possible for each project. By partnering with us, businesses can maximize their manufacturing budget and achieve cost-effective CNC machining solutions.
With the constantly evolving CNC machining market, businesses must stay informed and adaptable. By keeping an eye on market trends and economic factors, businesses can remain competitive and make informed decisions about their CNC machining projects. At Precision Machining Pro, we are committed to staying up-to-date with the latest advancements in the industry. Our dedication to innovation and efficiency ensures that our clients receive the most cost-effective and high-quality CNC machining services available.
In summary, optimizing CNC machining costs requires a comprehensive understanding of the various price factors, careful consideration of design and material choices, and effective utilization of skilled labor and technology. By implementing these strategies and partnering with a reputable CNC machining provider like Precision Machining Pro, businesses can achieve cost-efficient solutions and successfully navigate the dynamic landscape of the CNC machining industry.
FAQ
What are the factors that impact CNC machining prices?
The factors that can impact CNC machining prices include the number of parts being produced, the design features of the parts, the materials used, the tolerances required, the thickness of the parts, the size of the parts, and the impact of precision and speed on reducing time to market.
How does material selection influence CNC machining prices?
The type of material used for CNC machining can significantly impact the price. High-performance materials like titanium or stainless steel are more expensive compared to plastics or softer metals. The properties of the material, its machinability, and the current market pricing also play a role in determining material costs for CNC machining.
What role does design complexity play in CNC machining prices?
The complexity of the design can impact CNC machining prices. Intricate designs may require more advanced machinery, skilled operators, and extended machining times, all of which contribute to higher costs. However, complex designs can also result in higher precision and better product performance, so it’s essential to balance design complexity with budget considerations.
How does production volume affect CNC machining costs?
Production volume plays a crucial role in CNC machining costs. As production volumes increase, economies of scale come into play, making each part less expensive due to the spread of fixed charges like setup and tooling over more units. Finding the right balance between volume and setup efficiency is crucial for optimizing CNC machining costs.
How does machining time impact CNC pricing?
The time it takes to machine a part has a direct impact on the cost of CNC machining. Longer machining times, including setup time and actual cutting time, result in higher costs. Complex parts and intricate designs often require more setup time and extended machining times, increasing expenses. Finding efficiency in CNC machine cycle times is crucial for reducing costs.
How does skilled labor influence CNC machining costs?
Skilled labor is a significant factor that influences CNC machining costs. Proficient operators who are knowledgeable in CNC setup, programming, and operation are essential for accurate and productive machining. The cost of skilled labor contributes to the overall expenses. Effective utilization of skilled labor is crucial for striking a balance between budget control and leveraging the expertise of skilled personnel.
What is the impact of different CNC machine types on costs?
Different types of CNC machines, such as CNC milling machines, CNC lathes, CNC routers, and CNC plasma cutters, have varying price ranges and capabilities. Understanding the price range of diverse CNC machinery is essential for accurately estimating CNC machining costs. The upfront cost of a CNC machine and its expected yearly usage hours play a role in determining the machine shop rates.
Are there any additional costs associated with CNC machining?
Yes, there may be additional costs associated with the CNC machining process. These costs can include machine tool costs, surface finish costs, and specialized tooling costs, among others. Careful consideration of these additional costs is important for managing expenses and ensuring cost-effective CNC machining.
What are the current trends in the CNC machining industry?
The CNC machining industry is influenced by various market trends and economic factors. These include the growth trajectory of the CNC machine market, the adoption of automation and robotic integration in CNC operations, and the need to adapt to technological advancements. Staying informed about these trends is important for businesses in the CNC machining industry to adapt and succeed in a changing market.