First time CNC machining may seem daunting, at Precision Machining we offer assistance at each stage from concept to final product if you need assistance. Precision Machining Pro, is your ultimate resource for all things CNC machined parts! If you’re new to ordering CNC machined parts, you’ve come to the right place. In this comprehensive guide, we’ll walk you through the entire process and provide you with the knowledge you need to make informed decisions when it comes to ordering your first CNC machined parts.
At Precision Machining Pro, we specialize in CNC machining services, and we are a trusted CNC parts manufacturer and machining company. Whether you need CNC prototyping, CNC milling services, or CNC turning services, we have you covered. Our team of experts is dedicated to delivering high-quality, precision-machined parts that meet your exact specifications.
Ordering CNC machined parts for the first time may seem daunting, but with the right guidance, it can be a smooth and successful experience. From understanding the basics of machined parts to choosing the right machining service and considering important factors like material selection and tolerances, we’ll cover it all.
Key Takeaways:
- Understanding the design process when ordering CNC machined parts for the first time CNC parts is crucial.
- Choosing the right CNC machining service is important for quality and precision.
- Consider factors like material selection and tolerances when ordering CNC machined parts.
- Precision Machining Pro is a trusted CNC parts manufacturer and machining company.
- We offer a range of services, including CNC prototyping, CNC milling, and CNC turning.
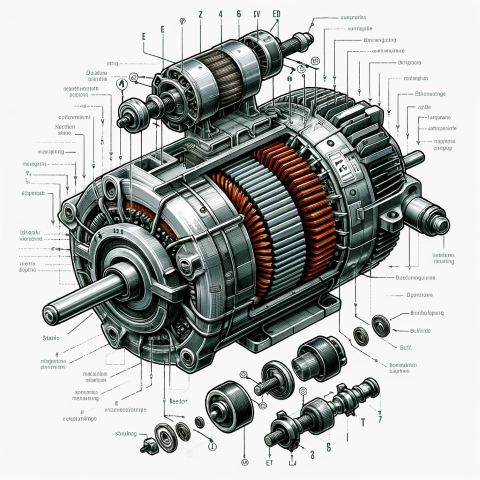
What are Machined Parts?
Machined parts are components fabricated using cutting machines such as mills, lathes, and routers. These machines use sharp cutting tools to cut sections away from a block of material known as the workpiece.
Machined parts can be made from a wide range of materials, including metals and plastics. They can be manually machined or digitally machined using CNC machines, which stands for Computer Numerical Control machines.
CNC machining is a precise and efficient method used to fabricate machined parts. It involves using computer-controlled cutting tools to remove material from the workpiece, resulting in accurate and high-quality components.
“[…] machining allows for the creation of complex shapes, tight tolerances, and high-quality surface finishes.” – Precision Machining Pro
The workpiece is secured in place while the cutting tools perform precise movements to shape and cut the material. This process can be used to create components of various sizes and complexities, from simple shapes to intricate parts with detailed features.
Whether a part is manually machined or digitally machined using CNC techniques, the end result is a machined part that meets specific dimensions and requirements.
Materials for Machined Parts
Machined parts can be made from a wide range of materials, depending on the desired characteristics and application. Common materials used for machined parts include:
Material | Properties | Common Applications |
---|---|---|
Metals (e.g., aluminum, steel, brass) | Durable, high strength, heat conductivity | Automotive, aerospace, machinery |
Plastics (e.g., ABS, acrylic, nylon) | Lightweight, corrosion resistance, flexibility | Consumer electronics, medical devices, prototyping |
Composites (e.g., carbon fiber, fiberglass) | High strength-to-weight ratio, stiffness | Sports equipment, aerospace, automotive |
Why Use Machined Parts?
Companies and professionals choose machined parts for their manufacturing needs due to the numerous advantages they offer. Machined parts are known for their strength and durability, making them ideal for applications that require robust components. They can also be designed with detailed features, allowing for intricate designs and precise functionality.
One of the key benefits of machined parts is the ability to work with a wide range of materials. Whether it’s metal, plastic, or even wood, these parts can be crafted to meet specific requirements and industry standards. This flexibility in material selection allows for greater customization and adaptability.
Another advantage of using machined parts is the ability to produce small quantities quickly and efficiently. This is particularly beneficial for companies that require prototypes or low-volume production runs. Machining processes offer a cost-effective solution for small-scale manufacturing.
Additionally, machined parts often meet industry-specific standards and certifications. This ensures that the components adhere to quality and safety regulations, making them suitable for various industries such as aerospace, automotive, and medical.
Machining is a tried-and-tested manufacturing technique that has been an industry standard for decades. Its reliability and precision make it a preferred choice for many manufacturing applications. Whether it’s for prototyping, production runs, or custom fabrication, machined parts offer the advantages of strength, detailed features, a wide range of materials, small quantities, and industry standards.
Advantages of Machined Parts
Machined parts offer several advantages over other manufacturing methods. These advantages make them a popular choice for a wide range of industries and applications. Here are some key benefits of using machined parts:
- No Minimum Order Quantity
One of the main advantages of machined parts is that there is no minimum order quantity requirement. This means that even small companies or individuals can order custom-machined parts without having to meet a certain quantity threshold. This makes machining a cost-effective option for prototyping or producing small batches of parts.
- Good Prototypes
Machining is often used for creating prototypes because it allows for the production of highly accurate and functional parts. This is especially important during the product development stage when designers need to test and validate their designs. Machined parts can be manufactured with tight tolerances and precise dimensions, allowing designers to evaluate their prototypes thoroughly.
- Design Freedom
With machining, designers have a lot of freedom when it comes to part design. Machined parts can be created in various shapes, sizes, and complexities. This design flexibility allows for the creation of highly customized parts that perfectly fit specific applications or meet unique requirements.
- Quality
Machined parts are known for their excellent quality. The machining process ensures high precision and accuracy, resulting in parts that meet tight tolerances. Additionally, machining allows for the use of a wide range of materials, including metals, plastics, and composites. This versatility enables designers to select materials that offer the best combination of strength, durability, and other desired properties for their parts.
- Fast Lead Times
When it comes to lead times, machining offers a significant advantage. CNC machines can produce parts quickly, especially when compared to other manufacturing methods such as casting or molding. This fast-production time is especially advantageous for companies that have tight project deadlines or need to quickly respond to changes in demand.
- Alterations on the Go
Another advantage of machined parts is the ability to make alterations during the production process. If design changes or improvements are required, they can be easily implemented in the machining program without the need for costly tooling modifications or additional setup time. This flexibility allows for iterative design processes, ensuring that the final product meets the desired specifications.
- Strength
Machined parts are known for their strength and durability. The machining process removes excess material and creates precise shapes, resulting in parts that have excellent structural integrity. This strength is crucial for applications where parts need to withstand high loads, vibrations, or harsh operating conditions.
- Surface Finish
Machined parts can have superior surface finishes compared to other manufacturing methods. CNC machines are capable of producing smooth and polished surfaces, which is important for applications that require aesthetic appeal or need to minimize friction or wear. The ability to achieve high-quality surface finishes ensures that machined parts meet both functional and visual requirements.
To further illustrate the advantages of machined parts, consider the following example:
Imagine you are a designer for a consumer electronics company. You need to develop a new smartphone casing that requires precise dimensions, intricate details, and a smooth surface finish. Machining would be the ideal manufacturing method for this application. Not only can you produce a good prototype for testing and evaluation quickly, but you also have the design freedom to create custom features and incorporate alterations during the production process. Additionally, the high-quality surface finish achieved through machining will give the smartphone a premium look and feel. With machined parts, you can ensure that your product not only meets the desired functional requirements but also stands out aesthetically in a competitive market.
Overall, machined parts offer numerous advantages, including design freedom, high quality, fast lead times, and the flexibility to make alterations on the go. These advantages make machining a reliable and efficient manufacturing method for a wide range of industries and applications.
Advantages of Machined Parts |
---|
No Minimum Order Quantity |
Good Prototypes |
Design Freedom |
Quality |
Fast Lead Times |
Alterations on the Go |
Strength |
Surface Finish |
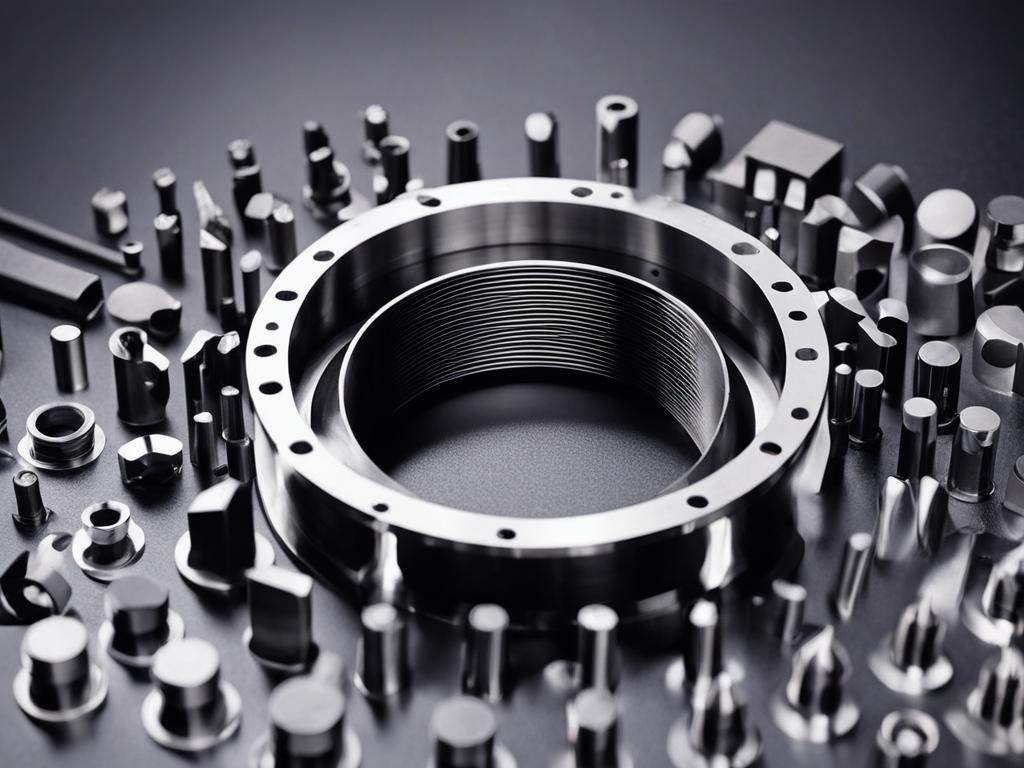
How to Design Machined Parts?
Designing machined parts involves considering manufacturing limitations and adhering to design for manufacturing principles. When designing your parts, it’s crucial to take into account factors such as undercuts, general tolerances, part tolerances, size limitations, and material selection. The complexity of the design and the use of 5-axis CNC machining can also impact the overall design process.
Design for Manufacturing
Design for manufacturing is the process of designing machined parts with the manufacturing process in mind. This approach ensures that the parts can be efficiently produced, minimizing costs and maximizing quality. By considering the capabilities and limitations of the CNC machine shop, you can optimize your design for manufacturing.
Undercuts
Undercuts are features of a part that the tool cannot directly access due to obstructions. When designing machined parts, it’s essential to consider undercuts and their impact on the manufacturing process. Complex undercuts may require additional setups or specialized tooling, increasing costs and production time.
General and Part Tolerances
Tolerances refer to the acceptable range of variation in dimensions for machined parts. General tolerances are the tolerances that apply to most dimensions, while part tolerances are specifications for specific features. Understanding these tolerances is crucial for ensuring the functionality and fit of the final product.
Size Limitations
Size limitations refer to the physical constraints of the CNC machine, such as the maximum dimensions it can accommodate. When designing machined parts, it’s important to consider these size limitations to ensure that your parts can be manufactured within the capabilities of the CNC machine shop you choose.
Material Selection
Choosing the right material for your machined parts is crucial for their performance and functionality. Consider factors such as the desired properties (e.g., strength, durability, heat resistance), manufacturability, and cost when selecting materials. The CNC machine shop can guide suitable material options.
Complexity and 5-Axis CNC Machining
The complexity of your design and the use of 5-axis CNC machining can impact the manufacturing process. Complex designs may require additional setups or specialized equipment, increasing costs and production time. 5-axis CNC machining offers increased flexibility and precision, allowing for more intricate and complex designs.
CNC Machine Shop Requirements
When choosing a CNC machine shop for your machining needs, it is crucial to consider their capabilities and requirements. By assessing these factors, you can ensure that your chosen machine shop is equipped to meet your specific project requirements and deliver high-quality results.
Here are some key aspects to evaluate when selecting a CNC machine shop:
Materials
First and foremost, consider the range of materials the machine shop specializes in. Different projects may require specific materials such as metals or plastics. Ensure that the machine shop has experience working with the materials you need for your project, as this will ensure a successful outcome.
Mass and Max Dimensions
Check the machine shop’s capabilities in terms of the mass and maximum dimensions they can handle. This will help determine if the machine shop is suitable for your project size. Whether you require small or large-scale production, knowing the machine shop’s limitations will enable you to make informed decisions.
Finishing Operations
Consider the finishing operations offered by the machine shop. Finishing touches such as surface treatments, coatings, or polishing may be essential for the final appearance and functionality of your parts. Ensure that the machine shop provides the necessary finishing operations to meet your requirements.
Precision
Precision is a crucial factor in CNC machining. Assess the precision capabilities of the machine shop’s equipment, such as the accuracy and repeatability of their machines. This is particularly important for projects that require tight tolerances or complex geometries.
Number of Machine Tools
The number of machine tools available in a CNC machine shop can provide insight into their capacity and ability to handle multiple projects simultaneously. A machine shop with a diverse range of machine tools can accommodate a variety of project requirements and ensure efficient turnaround times.
By evaluating these CNC machine shop requirements, you can select a reliable partner that aligns with your project needs and specifications. One such reputable CNC machine shop is Precision Machining Pro, distinguished for its expertise and commitment to precision machining.
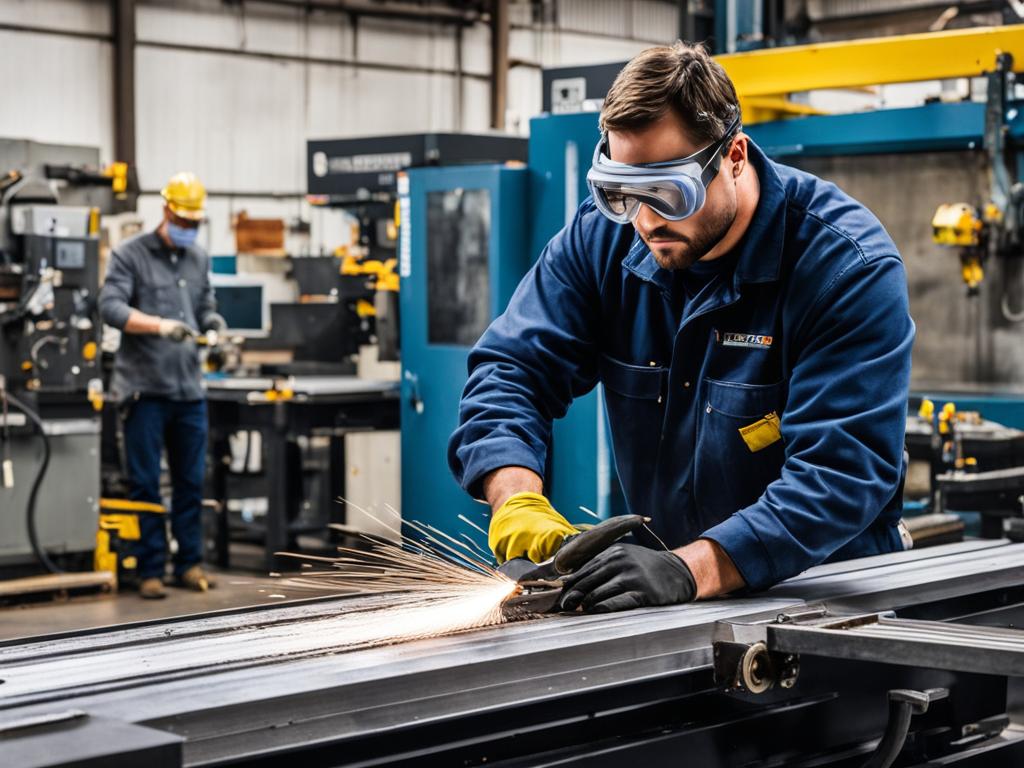
Next, we’ll delve into the design of ideal CNC parts, exploring the process of transforming concepts into tangible designs.
The Design Idealized for First Time CNC Parts Manufacturing
The design process for CNC parts starts with creating a concept and outlining the features of the product. This initial step allows you to have a clear vision of what you want to achieve with your CNC parts. Whether you are designing a complex mechanical component or a simple custom part, it is important to define the purpose and functionality of your design.
“Design is not just what it looks like and feels like. Design is how it works.” – Steve Jobs
With the concept in mind, the next step is to create a sketch that outlines the general layout and working principles of the part. A sketch serves as a visual representation of your design idea, allowing you to see its form and how different elements interact with each other. It provides a foundation for the 3D modeling phase by capturing the essential aspects of your design.
Once you have a well-defined sketch, you can begin the 3D modeling process using Computer-Aided Design (CAD) software. CAD software provides a digital platform for creating accurate and detailed 3D models of your CNC parts. It allows you to precisely define dimensions, angles, and other specifications of your design. With CAD software, you can easily modify and iterate on your design, ensuring that it meets your requirements.
“Design is a solution to a problem. Art is a question to a problem.” – John Maeda
With numerous free lessons available online, acquiring the skills needed for 3D modeling has never been more accessible. You can find tutorials and resources that cater to beginners as well as more advanced designers. By familiarizing yourself with the tools and techniques of 3D modeling, you can bring your design to life and prepare it for the manufacturing process.
Design Process | Description |
---|---|
Create a Concept | Define the purpose and functionality of your design. |
Create a Sketch | Outline the general layout and working principles of the part. |
Make a 3D Model | Use CAD software to create a precise and detailed digital representation of your design. |
Modifying Design for Manufacturing CNC Parts Needs
Once you have created an idealized design for your CNC parts, the next crucial step is to modify it for manufacturing. This involves considering the capabilities of the CNC machine shop you have chosen and making any necessary changes to your design. By doing so, you can ensure that your design can be successfully produced and maximize the efficiency of the manufacturing process.
Modifying your design for manufacturing involves several important considerations. Even small changes to the design can have a significant impact on cost reduction and improved efficiency. By optimizing your design for manufacturing, you can minimize material waste, reduce production time, and enhance overall quality.
Seeking manufacturing advice is crucial during this stage. By consulting with experts at the CNC machine shop, you can gain valuable insights and recommendations on how to improve your design. Their expertise can help you identify potential design flaws, suggest specific design changes, and provide guidance on material selection and manufacturing best practices.
Improving your design is not only about making it manufacturable but also about considering future production scalability. By anticipating potential scalability challenges, you can make design adjustments that ensure smooth production and allow for easy scaling as demand increases.
Key Factors to Consider when Modifying your Design
- Design conversion: Adapt your design to the specific requirements and capabilities of the CNC machine shop.
- Manufacturing advice: Consult with experts to receive valuable insights and recommendations on improving your design.
- Cost reduction: Make design changes that minimize material waste and optimize production efficiency.
- Improving design: Enhance the manufacturability and functionality of your design through strategic modifications.
- Changes to the design: Consider necessary alterations to ensure a successful manufacturing process.
By focusing on these factors and collaborating closely with the CNC machine shop, you can create a design that not only meets your requirements but is also optimized for efficient and cost-effective production.
Remember, even minor design adjustments can lead to significant improvements in manufacturing outcomes. Don’t hesitate to seek guidance and make the necessary changes to achieve the best possible results.
CNC Programming
Once the design is finalized, the next step is CNC programming. This crucial step involves creating a CNC program that instructs the machine tooling’s movement. The CNC program is written using G-code or M-code, which are standardized programming languages for CNC machines.
To simplify the programming process, designers can utilize Computer-Aided Manufacturing (CAM) systems. These systems provide a user-friendly interface for generating the CNC program based on the specific requirements of surface machining and cutting tool dimensions. With the help of CAM systems, designers can ensure accurate and efficient manufacturing processes.
“Effective CNC programming is essential to achieve precise and high-quality machined parts.”
In addition to controlling the movement of the machine tooling, the CNC program also includes instructions for various machining operations such as milling, drilling, and turning. It specifies tool paths, cutting speeds, and feed rates to ensure the desired surface finish and dimensional accuracy of the machined parts.
Here is an example of a CNC program written in G-code:
G90 ; Set to absolute positioning
G01 X10 Y10 ; Rapid move to coordinate (10, 10)
G01 Z0 ; Rapid move to Z-axis position 0
G01 X20 Y20 ; Linear move to coordinate (20, 20)
Cutting Tool Dimensions
It is crucial to consider the dimensions of the cutting tools when creating the CNC program. The cutting tools must be selected based on the design requirements and the material being machined.
The dimensions of the cutting tools include the tool’s diameter, length, and shape. These parameters directly affect the accuracy of the machining process and the final quality of the machined parts. Using incorrect cutting tool dimensions can lead to dimensional errors, poor surface finish, and even tool breakage.
Designers should refer to tool catalogs or consult with tooling suppliers to ensure the selection of appropriate cutting tools for their CNC machining operations.
Cutting Tool Dimension | Description |
---|---|
Tool Diameter | The width of the cutting tool’s active cutting surface. |
Tool Length | The overall length of the cutting tool, including the shank and cutting portion. |
Tool Shape | The geometric shape of the cutting tool, such as square, cylindrical, or ball-end. |
By carefully considering the cutting tool dimensions and incorporating them into the CNC program, designers can ensure precise and accurate machining, resulting in high-quality machined parts.
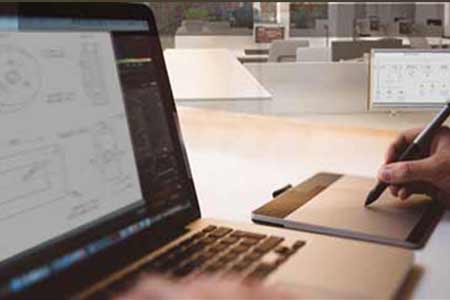
Next, we will discuss the CNC machine setup, which involves determining the part orientation, clamping, coordinating zero setting, and loading the cutting tools.
CNC Machine Setup
Before machining the part, the CNC machine needs to be set up. This crucial step ensures the accurate machining of the part and the successful execution of the CNC program. Paying attention to detail during the setup process will yield high-quality results. Here are the essential steps to follow:
Part Orientation
Proper part orientation is vital to ensure that the machining operations are performed correctly. Determine the correct positioning of the part within the machine, taking into account any required tool access or specific machining requirements.
Part Clamping
Securely clamping the part is crucial to prevent movement during machining. Use appropriate clamping techniques to ensure the part remains firmly in place, minimizing the risk of errors or inaccuracies.
Coordinate Zero
Setting the coordinate zero accurately establishes the origin point from which all machining operations are referenced. This zero point serves as a reference for tool paths and ensures consistency across multiple machining operations.
Loading Cutting Tools
Loading the cutting tools into the machine is the final step before initiating the machining process. Ensure the correct tools are selected based on the specific machining requirements and securely install them in their respective holders or tool changers.
By meticulously executing these steps, you create a foundation for successful CNC machining. Next, we will explore the CNC programming process, where we define the precise instructions for the machine to follow based on our design.
Step | Description |
---|---|
Part Orientation | Determine the correct positioning of the part within the machine. |
Part Clamping | Securely clamp the part to prevent movement during machining. |
Coordinate Zero | Set the coordinate zero accurately to establish the origin point. |
Loading Cutting Tools | Select and install the appropriate cutting tools for the machining operation. |
Final Thoughts
Ordering CNC machined parts for the first time can be a complex process, but with Precision Machining Pro, it’s never been easier to get started with CNC parts ordering. By following the steps outlined in this guide, you can ensure a successful and efficient experience. From understanding the basics of machined parts to designing and programming the CNC machine, each step is important in achieving high-quality results.
When it comes to custom CNC machining, Precision Machining Pro offers top-notch services. With their state-of-the-art equipment and expertise, they can deliver precision machined parts that meet your specific requirements. Whether you need a prototype or a large batch order, their online CNC machining platform makes it convenient and hassle-free to place your order.
By choosing Precision Machining Pro, you can have confidence in the quality and consistency of your CNC machined parts. They take into account important factors such as material selection and tolerances, ensuring that your parts are made to the highest standards. With their attention to detail and commitment to customer satisfaction, you can expect precision and accuracy in every order.
So, whether you’re new to CNC machining or looking for a reliable partner for your custom-machined parts, getting started with CNC parts ordering has never been easier. Visit Precision Machining Pro at http://precisionmachiningpro.com to explore their services and take the first step towards producing high-quality CNC machined parts.
FAQ
What are machined parts?
Machined parts are components fabricated using cutting machines such as mills, lathes, and routers. These machines use sharp cutting tools to cut sections away from a block of material known as the workpiece.
Why use machined parts?
Machined parts offer excellent strength, can have detailed features, and can be made from a wide range of materials. They are suitable for producing small quantities quickly and often meet industry-specific standards and certifications.
What are the advantages of machined parts?
Machined parts have no minimum order quantity, and offer design freedom, high quality, fast lead times, the ability to make alterations on the go, and excellent strength and surface finish.
How should I design machined parts?
When designing machined parts, considerations include manufacturing limitations, factors such as undercuts, general tolerances, part tolerances, size limitations, and material selection. Complexity and the use of 5-axis CNC machining can also impact the design process.
What are the requirements for a CNC machine shop?
When choosing a CNC machine shop, it is important to consider their capabilities and requirements. This includes looking at the materials they work with, the mass and max dimensions of the parts they can make, the finishing operations they offer, the precision of their equipment, and the number of different machine tools they have.
How do I create an idealized design for CNC parts?
The design process for CNC parts starts with creating a concept and outlining the features of the product. This is followed by creating a sketch that outlines the general layout and working principles of the part. From there, designers can start making a 3D-model of their design using CAD software.
How do I modify a design for manufacturing CNC parts?
Once the design is finalized, designers need to consider the manufacturing capabilities of the chosen CNC machine shop and make necessary changes to their design if required. Even small changes in the design can lead to cost reduction and improved efficiency. Designers should also seek manufacturing advice and consider the potential for future production scalability.
How do I program CNC parts?
CNC programming involves creating a CNC program using G-code or M-code, which controls the movement of the machine tooling. Designers can use CAM systems to generate the CNC program based on the surface machining requirements and the dimensions of the cutting tools.
What is involved in CNC machine setup?
Before machining the part, the CNC machine needs to be set up. This involves determining the part orientation, securely clamping the part, setting the coordinate zero, and loading the cutting tools into the machine.
How do I get started with ordering CNC machined parts?
To get started with ordering CNC machined parts, it is important to understand the basics of machined parts, design considerations, CNC programming, and CNC machine setup. By choosing the right CNC machine shop and considering factors such as material selection and tolerances, users can ensure precision and satisfaction with their CNC machined parts.