Machining shop size matters for the following 5 reasons.
- Maximized equipment utilization and increased production throughput
- Ability to accommodate a wider range of part sizes and complexities
- Improved workflow management and minimized bottlenecks
- Reduced production time and faster turnaround
- Enhanced overall efficiency and cost-effectiveness
Choosing a machining shop the machining shop size may impact both the quality and price.
When it comes to CNC machining, the size of the shop truly matters. The scale and capabilities of a machining shop can have a significant impact on the success and efficiency of your precision machining projects. Understanding the possibilities and limitations of different shop sizes is crucial for ensuring optimal results.
There are thousands of different machining shops from single operators to 100’s of machines.
CNC machining involves the use of computer-controlled machines to produce high-quality and precise parts. These machines can perform a wide range of operations, from cutting and shaping to drilling and milling. However, the size of the shop plays a vital role in determining what can be achieved.
The size of the shop directly affects the work envelope of the machining center, which refers to the dimensions of the machine’s travel. It also influences the sizing considerations for CNC lathe parts and the available post-processing options. Additionally, electrical capacity and 3-phase power play essential roles in the functioning and productivity of a CNC shop.
In this article, we will explore the key factors related to CNC machining shop size and their impact on precision machining projects. We will discuss the work envelope of machining centers, sizing considerations for CNC lathe parts, post-processing options, electrical capacity, and the value of 3-phase power. Furthermore, we will provide tips for training CNC operators, challenges and solutions for hiring operators, discuss the benefits of optimizing shop size, and take a glimpse into future trends in CNC machining shop size.
Key Takeaways:
- The size of a CNC machining shop can greatly impact the outcome and efficiency of precision machining projects.
- The work envelope of a machining center determines the machine’s travel dimensions and affects the maximum part dimensions that can be accommodated.
- CNC lathe parts have specific size limitations, such as maximum part diameter and overall length.
- The size of a part can influence the availability of post-processing options.
- Electrical capacity and 3-phase power are crucial considerations for optimal CNC shop operation.
Understanding the Work Envelope of a Machining Center
The work envelope is a critical aspect to consider when operating a machining center. It refers to the machine’s travel dimensions, which determine the maximum size and complexity of the parts that can be produced. By understanding the work envelope, you can effectively plan and execute your CNC machining projects.
Xometry’s partner network includes a wide range of CNC machining centers, each with specific travel limitations. For example, some machining centers may have a work envelope of 64″ (X) by 32″ (Y) by 38″ (Z). These dimensions represent the maximum distance that the machine’s spindle can travel along each axis.
It’s important to note that the travel limitations of a machining center do not necessarily translate to the maximum part dimensions that can be produced. Deep features requiring long tooling can reduce the effective work envelope of a machine. Therefore, it is crucial to consider the total dimensions of your parts and their specific features to ensure they can be accommodated within the work envelope of the machining center.
Understanding the work envelope of a machining center allows you to select the right equipment and plan your machining operations effectively. By working within the specified travel limitations and considering the complexities of your parts, you can achieve precise and efficient CNC machining results.
Sizing Considerations for CNC Lathe Parts
When it comes to CNC lathe parts, it is essential to consider the critical limiting dimensions of the maximum part diameter and overall length. These factors play a significant role in determining the feasibility and success of your CNC lathe projects.
Xometry, a leading provider of CNC machining services, supports parts with a maximum diameter of 18 inches. However, for larger parts, special considerations can be made to accommodate your specific requirements and project needs.
The maximum overall length that can be supported also depends on the part’s maximum diameter. It is important to note that live tooling lathes, which enable the machining of more complex turned parts with off-axis features, often have smaller effective work envelopes. This means that the overall length of the part may need to be adjusted to fit within the machine’s capabilities.
Considering the CNC lathe part diameter and overall length is crucial for ensuring the successful completion of your machining projects. By understanding these sizing considerations, you can collaborate effectively with CNC machining experts to achieve the desired results.
To further illustrate the range of part sizes supported by Xometry, refer to the table below:
Maximum Part Diameter | Maximum Overall Length |
---|---|
Up to 18 inches | Dependent on part diameter |
Impact of Part Size on Post-Processing Options
The size of a part can have a significant impact on the available post-processing options in CNC machining. When planning for post-processing operations, it is crucial to consider the size of your parts to ensure compatibility and feasibility.
For instance, larger parts may pose challenges when it comes to media blasting. They may not fit in standard media-blasting cabinets, requiring alternative solutions or larger equipment.
“The size of your parts matters when it comes to post-processing operations.”
Another consideration is custom racking requirements for processes like anodizing or electroplating. Larger parts may need specific racking setups to ensure proper coating application and evenness.
To accommodate post-processing needs effectively, it is essential to evaluate the size of your parts during the planning stage. This consideration will help ensure that you have the necessary resources and options available for completing post-processing operations.
The following table provides an overview of the impact of part size on various post-processing options:
Part Size | Media Blasting | Anodizing | Electroplating |
---|---|---|---|
Small | Compatible | Compatible | Compatible |
Medium | Compatible | Compatible | Compatible |
Large | May require larger equipment or alternative solutions | May require custom racking | May require custom racking |
Understanding the impact of part size on post-processing options is vital for determining the most suitable approaches for your CNC machining projects. By considering the size of your parts, you can ensure efficient and successful post-processing operations.
Importance of Electrical Capacity for CNC Shops
When it comes to running a CNC shop, electrical capacity is a critical consideration. The smooth and efficient operation of your shop relies on having the right electrical setup in place.
For a commercial setup, CNC shops typically require a minimum electrical capacity of 400 amps. This ensures that the equipment can function optimally and handle the power demands of various machining processes. However, if your shop’s requirements exceed this threshold, it may be necessary to involve an electrical engineer to assess and address the increased capacity needs.
One key aspect of electrical capacity is the choice of voltage system. A 240v 3-phase electrical system is often preferred in CNC shops. This system provides sufficient power to operate multiple machines simultaneously and eliminates the need for step-up or step-down transformers. By utilizing a 3-phase power setup, you can streamline your electrical infrastructure and avoid potential inefficiencies and equipment compatibility issues.
Considering the electrical needs of your CNC shop is vital for ensuring operational efficiency and avoiding potential downtime due to electrical limitations. It is recommended to consult with electrical professionals who specialize in industrial and commercial setups to design an electrical system that meets your shop’s specific requirements.
The Value of 3-Phase Power in CNC Machining
When it comes to CNC machining, having the right electrical capacity is crucial for optimal performance. One of the key elements to consider is the use of 3-phase power.
3-phase power is highly beneficial for CNC machining operations due to its higher power capacity compared to single-phase systems. This increased capacity allows for more efficient and reliable operation of CNC equipment, resulting in improved productivity and reduced downtime.
Many CNC machines, such as welders and computer systems, are designed to work best on 3-phase power. By providing a consistent and stable power supply, 3-phase power ensures smooth and accurate operation of these machines, minimizing the risk of electrical fluctuations that can disrupt the machining process.
Investing in a 3-phase power setup for your CNC shop is an excellent way to optimize productivity and maintain a competitive edge in the machining industry. With the ability to handle larger loads and power multiple machines simultaneously, 3-phase power enables you to take on more complex projects and meet higher production demands with ease.
Furthermore, 3-phase power is often more cost-effective in the long run. While the initial setup cost may be higher than a single-phase system, the efficiency gains and reduced energy consumption can result in significant savings over time.
Overall, the value of 3-phase power in CNC machining cannot be overstated. It provides the necessary electrical capacity for optimal performance and offers numerous benefits, including improved productivity, reliability, and cost-effectiveness.
Benefits of 3-Phase Power in CNC Machining |
---|
Higher Power Capacity: 3-phase power enables CNC machines to handle larger loads and power multiple machines simultaneously. |
Efficient Operation: The stable and consistent power supply of 3-phase power ensures smooth and accurate operation of CNC equipment. |
Improved Productivity: With the ability to handle more complex projects and meet higher production demands, 3-phase power allows for increased productivity. |
Reduced Downtime: The reliability of 3-phase power minimizes the risk of electrical fluctuations that can disrupt the machining process and cause downtime. |
Cost-Effectiveness: While the initial setup cost may be higher, 3-phase power is often more cost-effective in the long run due to efficiency gains and reduced energy consumption. |
Considerations for Setting up 3-Phase Power in a CNC Shop
Setting up 3-phase power in a CNC shop is a crucial step to ensure the smooth operation of your CNC equipment. This process involves collaborating with the local electric company and engaging an electrician for installation, as it requires specialized knowledge and expertise.
The first step is to contact your local electric company and discuss your electrical capacity needs. Your CNC shop will typically require a minimum of 400 amps for a commercial setup. The electric company may provide the service for free or offer incentives based on the projected electrical usage. Take advantage of these opportunities to optimize the power supply for your CNC shop.
During the installation process, your electrician may need to add transformers, upgrade panels, and connect phase converters if needed. These components help ensure the proper distribution of electricity and maximize the efficiency of your machinery. It is essential to work with professionals who are familiar with CNC shop electrical requirements and comply with electrical codes.
Once the 3-phase power setup is complete, you will benefit from a more stable and efficient power supply for your CNC machines. 3-phase power provides higher power capacity compared to single-phase systems, allowing your machines to operate at their full potential. It also eliminates the need for step-up or step-down transformers, simplifying your electrical setup.
Remember to regularly check your electrical system and perform maintenance to ensure optimal performance. This includes inspecting wiring, circuits, and connections to identify any potential issues that could disrupt your CNC shop’s operation.
By setting up 3-phase power in your CNC shop, you can avoid power-related disruptions and maximize the productivity of your machines. With a reliable electrical supply, you can focus on delivering high-quality CNC machining services to your customers.
Benefits of Setting up 3-Phase Power in a CNC Shop |
---|
1. Higher power capacity for efficient operation of CNC machines |
2. Elimination of the need for step-up or step-down transformers |
3. More stable power supply, reducing the risk of equipment damage |
4. Improved overall efficiency and productivity |
5. Reduced downtime and increased customer satisfaction |
Tips for Training CNC Operators on Sizing Adjustments
Training CNC operators on sizing adjustments is crucial for maintaining machining accuracy. Properly trained operators ensure that sizing adjustments are effectively managed during setup and production runs, resulting in precise and high-quality parts.
- Provide a Definition and Explanation of Sizing Adjustments: Start by introducing CNC operators to the concept of sizing adjustments. Explain that these adjustments are made to achieve the desired dimensions of a part and ensure that it meets the specified tolerances. Emphasize the importance of accuracy in machining and how sizing adjustments play a vital role in achieving it.
- Teach the Math Involved in Making Adjustments: Familiarize operators with the mathematical calculations necessary for sizing adjustments. This includes understanding how to calculate the required amount of material to be removed or added to achieve the desired dimensions. Provide practical examples and exercises to reinforce their understanding of the mathematical concepts involved.
- Practice Measurement Techniques: Training CNC operators on sizing adjustments should also include practicing precise measurement techniques. Teach them how to accurately use measuring tools such as calipers, micrometers, and height gauges. Emphasize the importance of consistently measuring and verifying part dimensions throughout the machining process.
- Teach Evaluation of Measured Attributes: Instruct operators on how to evaluate the measured attributes of a part and compare them to the required specifications. Show them how to identify any deviations and determine the appropriate sizing adjustments needed to correct them. Encourage them to pay attention to detail and develop a keen eye for detecting potential issues.
- Demonstrate How to Make Sizing Adjustments at the Machine: Finally, demonstrate to CNC operators how to make sizing adjustments directly at the machine. Walk them through the process of adjusting cutting paths, tool offsets, and other relevant parameters based on the measured attributes of the part. Encourage them to approach these adjustments with precision and care to achieve the desired dimensions.
By following these five key steps in training CNC operators on sizing adjustments, you can ensure that your machining processes maintain the highest levels of accuracy and quality. Well-trained operators are equipped with the knowledge and skills necessary for making precise sizing adjustments, leading to successful machining outcomes.
Challenges and Solutions for Hiring CNC Operators
Finding qualified CNC operators can be challenging for companies. With a limited pool of skilled operators, many companies are hiring individuals with limited or no shop experience and training them from scratch. This approach presents its own challenges as new hires need to learn the intricacies of CNC machining and develop the necessary skills.
To address this challenge, companies can implement comprehensive training programs that cover the fundamentals of CNC machining. These programs can include theoretical lessons on machine operations, programming, and tooling, as well as practical hands-on experience with CNC machines. By offering a combination of classroom instruction and on-the-job training, companies can ensure that their CNC operators acquire the necessary knowledge and skills to excel in their roles.
Additionally, partnering with local vocational schools or technical colleges can be an effective solution for attracting new talent and providing them with the relevant education and training. This not only helps companies in their recruitment efforts but also contributes to the development of a skilled workforce in the CNC machining industry.
Investing in training and development is crucial for building a capable CNC operator team. By providing ongoing educational opportunities and career advancement prospects, companies can attract and retain talented individuals who are passionate about CNC machining.
Challenges | Solutions |
---|---|
Limited pool of skilled operators | Implement comprehensive training programs |
Training individuals with limited or no shop experience | Provide hands-on experience and on-the-job training |
Attracting new talent | Partner with vocational schools or technical colleges |
Ensuring retention of skilled operators | Offer ongoing educational opportunities and career advancement prospects |
Benefits of CNC Machining Shop Size Optimization
Optimizing the size of your CNC machining shop can offer numerous benefits that enhance your overall operations. By strategically determining the most efficient size for your shop, you can maximize productivity, accommodate a wider range of part sizes and complexities, and streamline your workflow management. This optimization process ultimately leads to reduced production time and improved efficiency throughout your CNC machining operations.
One of the key advantages of size optimization is the ability to efficiently utilize your equipment. With a well-sized shop, you can fully leverage your CNC machines, ensuring they are operating at their optimal capacity. This not only increases your production throughput and capacity but also allows you to handle larger and more complex machining projects with ease.
Effective shop size optimization also plays a crucial role in workflow management. By aligning your shop size with your production needs, you can enhance the efficiency of material flow, minimize bottlenecks, and optimize the layout of your equipment. This leads to smoother operations, reduced downtime, and improved overall productivity.
Reducing production time is another significant benefit of CNC machining shop size optimization. With a well-designed and properly sized shop, you can minimize the time spent on material handling and tool changeovers, increasing the overall speed of your machining processes. This translates to shorter lead times and faster turnaround for your customers, enabling you to meet tight deadlines and gain a competitive edge in the market.
Ultimately, optimizing your CNC machining shop size improves the overall efficiency of your operations. The streamlined workflow, increased equipment utilization, and reduced production time all contribute to enhanced productivity and cost-effectiveness. By investing the time to determine the optimal size for your shop, you can enjoy these long-term benefits that positively impact your bottom line.
Additional Benefits of CNC Machining Shop Size.
Purchasing power for materials.
The smaller the operators, the less likely they have the materials in stock. Increasing the likelihood they, will need to pay more for the raw materials.Purchasing larger quantities usually gives the bigger companies an advantage. When purchasing the raw materials needed for the projects.
The bigger Machine shops, usually carry stock of standard or often used materials.
This can have effects on the prices of materials and ultimately the cost of the machined parts.
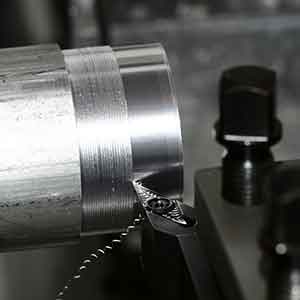
Project set up.
While smaller business operators usually have a lot of experience from doing varied projects.
They generally rely more on previous experience and training to set up the machines.
Most larger businesses have dedicated CAD/CAM systems and operators, With a management structure allowing them to easily plan the efficient use of the materials and machine time. Because of the greater number of projects both completed and underway, they have a varied experience with the newer style of projects.
Types of Machines and Tooling.
The machines are the biggest investment in any Machining shop.
Second to the machines is the tooling required for a project.
Machining parts can use a variety of machines to get the best result.
Some smaller operators have to make do with older machines and in some cases get some of the work done outside their workshop.
Tooling may be needed for just one project and can be very expensive.
Larger operators will generally have a variety of machines choosing the lowest-cost cnc services to process the parts.
Machine shops generally have a big selection of tooling that can be used on various projects.
Saving both time and money.
Operators experience.
Smaller operators usually have varied types of projects and can be more experienced with a range of projects.
Their projects can be limited in scope according to the machines and the time spent on a type of project.
Larger workshops have more operators with greater experience with individual types of projects.
The operators usually spend more time on a single type of machine.
This enables them to program the machine for the project more efficiently since they are aware of the small differences between machines.
Quality checking and other services.
Depending on the Machining of the parts, the devices required to check can vary.
Smaller operators usually have limited access to high grade very precise instruments.
In many cases, they would need to send work out for some additional finishes or options.
Such as Laser etching, Anodizing, heat treatment in some cases even polishing.
Larger companies could have in-house 3d checking machines to ensure the project meets the exact specifications.
They could also have additional services in-house for laser etching to help categorize parts or add branding to the finished parts.
Many people believe using smaller operators will save money. While it is possible it is not always the case even for small projects.
Get your free Quotation
At Precision Machining Pro, we offer the latest machining service.
Fast quote and prompt machining of your parts or project.
[button link=”http://precisionmachiningpro.com/cnc-machining-quotation/” type=”big”] GET my FREE Quote now[/button]
Benefits | Description |
---|---|
Maximized equipment utilization and increased production throughput | By optimizing your shop size, you can efficiently leverage your CNC machines, resulting in higher production throughput and capacity. |
Ability to accommodate a wider range of part sizes and complexities | A properly sized shop enables you to handle larger and more complex machining projects without limitations. |
Improved workflow management and minimized bottlenecks | Optimizing your shop size ensures smoother material flow and minimizes bottlenecks, enhancing overall workflow efficiency. |
Reduced production time and faster turnaround | An optimized shop size allows for faster material handling and tool changeovers, resulting in reduced production time and faster project turnaround. |
Enhanced overall efficiency and cost-effectiveness | Well-sized CNC machining shops streamline operations, leading to increased efficiency and improved cost-effectiveness for your business. |
Future Trends in CNC Machining Shop Size
As technology continues to advance and the demands of the manufacturing industry evolve, CNC machining shop size is expected to follow suit. Industry trends indicate a shift towards smaller, more compact CNC machines that occupy less floor space while maintaining exceptional precision and capabilities. This transition allows businesses to optimize their shop layouts and utilize their available space more efficiently.
Additionally, automation and robotics are expected to play a significant role in the future of CNC machining. By incorporating automated systems into their workflow, shops can streamline operations, reduce labor costs, and improve overall production efficiency. These advancements in automation technology enable CNC machining shops to handle larger workloads and meet increased customer demands.
By staying informed and keeping abreast of these future trends, CNC machining shops can position themselves competitively in the industry. Adopting smaller, more efficient machines and integrating automation and robotics into their processes can provide companies with a competitive advantage, ensuring they can meet the evolving needs of their customers.
As CNC machining continues to evolve, businesses need to keep up to date with future trends to remain at the forefront of the industry. By staying flexible and open to new technologies and approaches, CNC machining shops can thrive in an ever-changing manufacturing landscape.
Conclusion
In conclusion, the size of a CNC machining shop is a crucial factor that significantly impacts the success of precision machining projects. The capabilities and equipment scale of a shop directly influence the outcome and overall efficiency of CNC machining operations. Understanding the limitations and possibilities of different shop sizes allows businesses to optimize their processes and achieve successful project outcomes.
One key consideration is the electrical capacity of the CNC shop. Ensuring adequate electrical capacity, with a minimum of 400 amps for a commercial setup, is essential for maintaining operational efficiency. Investing in a 3-phase power setup further enhances productivity and allows for the effective operation of CNC equipment.
Training CNC operators on sizing adjustments is also crucial to maintain machining accuracy. Proper training in measurement techniques, evaluation of measured attributes, and making sizing adjustments at the machine ensures that operators can effectively manage adjustments during setup and production runs.
Optimizing the size of a CNC machining shop offers numerous benefits. It enables efficient equipment utilization, maximizes production throughput, and accommodates a wide range of part sizes and complexities. With a properly optimized shop size, businesses can enhance workflow management, reduce production time, and improve overall efficiency.
In conclusion, considering CNC machining shop size, electrical capacity, operator training, and overall optimization are essential factors for maximizing the benefits of CNC machining. By carefully evaluating these aspects, businesses can ensure successful project outcomes and stay competitive in the precision machining industry.
Summary FAQ
How does CNC machining shop size impact precision machining projects?
CNC machining shop size plays a crucial role in precision machining projects. The capabilities and equipment scale of a shop can greatly impact the outcome and efficiency of your CNC machining needs.
What is the work envelope of a machining center?
The work envelope of a machining center refers to the machine’s travel dimensions. It is important to understand the limitations and possibilities of different shop sizes to ensure your projects are executed successfully.
What are the sizing considerations for CNC lathe parts?
The critical limiting dimensions for CNC lathe parts are the maximum part diameter and overall length. Different machines support various part sizes, and special considerations can be made for larger parts.
How does part size impact post-processing options?
The size of a part can affect the availability of different post-processing operations. Larger parts may require specific arrangements for processes such as media-blasting, anodizing, or electroplating.
Why is electrical capacity important in a CNC shop?
Electrical capacity is crucial for a CNC shop. It affects the operational efficiency and power requirements of the equipment. It is important to consider the electrical needs of your CNC shop to ensure smooth operations.
What are the benefits of using 3-phase power in CNC machining?
3-phase power is highly beneficial for CNC machining operations. It provides higher power capacity, enhances efficiency, and enables more reliable operation of CNC equipment. It is worth investing in a 3-phase power setup for your CNC shop to optimize productivity.
How can 3-phase power be set up in a CNC shop?
Setting up 3-phase power in a CNC shop involves collaborating with the local electric company and engaging an electrician for installation. It may require adding transformers, upgrading panels, and connecting phase converters if needed.
How can CNC operators be trained on sizing adjustments?
Training CNC operators on sizing adjustments is crucial for maintaining machining accuracy. The training process typically involves providing definitions and explanations, teaching the math involved, practicing measurement techniques, and demonstrating adjustment methods.
What are the challenges and solutions for hiring CNC operators?
Finding qualified CNC operators can be challenging. However, companies can address this challenge by implementing comprehensive training programs and providing hands-on experience to develop the necessary skills.
What are the benefits of optimizing CNC machining shop size?
Optimizing the size of a CNC machining shop can yield various benefits. It allows for efficient equipment utilization, maximizes production throughput, accommodates a range of part sizes and complexities, and improves overall workflow management and efficiency.
What are the future trends in CNC machining shop size?
As technology advances, the future of CNC machining shop size is expected to witness smaller, more compact CNC machines that take up less floor space while maintaining high precision and capabilities. Automation and robotics may also be integrated to optimize workflows and improve production efficiency.
Why does CNC machining shop size matter?
CNC machining shop size matters significantly in precision machining projects. It impacts the capabilities, equipment scale, and overall efficiency of CNC machining operations. By understanding the limitations and possibilities of different shop sizes, businesses can optimize their CNC machining processes and achieve successful project outcomes.
Source Links
- https://www.mmsonline.com/articles/5-things-cnc-operators-must-know-about-sizing-adjustments
- https://www.xometry.com/resources/machining/3-things-to-know-about-size-limitations-for-cnc-machining/
- https://www.practicalmachinist.com/forum/threads/power-requirements-for-a-small-shop.245248/