Welcome to Precision Machining Pro, where we delve into the world of CNC machining and explore the best surface finishes for your projects. Surface finishing is a crucial step in CNC machining, offering a multitude of benefits, from enhancing the appearance of your parts to improving their strength, resistance, and electrical conductivity. In this article, we will examine the various surface finish options available and help you make informed decisions for your CNC machining needs.
Key Takeaways:
- Surface finishing is the final step in CNC machining and provides various benefits.
- As-machined finishes offer tight dimensional tolerances and affordability but lack protection.
- Anodizing thickens the oxide layer, providing durability and corrosion resistance.
- Powder coating creates a protective layer and is compatible with all metals.
- Bead blasting adds a matte or satin finish for aesthetic purposes.
As-Machined Finishes for CNC Machining
In CNC machining, as-machined finishes are the default option for surface finishing. These finishes have small tool marks and blemishes, resulting in an average surface roughness of around 3.2 μm. As-machined parts offer tight dimensional tolerances and are affordable to produce since post-processing is not required.
We at Precision Machining Pro prioritize dimensional integrity when using as-machined finishes, ensuring that the final parts meet the required specifications with precision. The affordability of these finishes makes them an attractive choice for projects with budget constraints.
However, it’s important to note that as-machined finishes lack the protective coatings provided by other finishing options. This makes the parts susceptible to nicks, scuffs, and scratches, particularly in high-wear or corrosive environments.
When selecting as-machined finishes for CNC machining, it is crucial to consider the specific requirements and application of the parts. If protection and aesthetics are secondary concerns and tight dimensional tolerances are of utmost importance, as-machined finishes are a suitable choice.
Advantages of As-Machined Finishes
Advantages of as-machined finishes for CNC machining include:
- Tight dimensional tolerances: As-machined finishes offer precise dimensional accuracy, ensuring that the parts meet the required specifications.
- Affordability: As-machined finishes are cost-effective since they eliminate the need for additional post-processing steps, making them an economic choice for projects with budget constraints.
Disadvantages of As-Machined Finishes
Disadvantages of as-machined finishes for CNC machining include:
- Lack of protection: As-machined finishes do not provide protective coatings, making the parts susceptible to nicks, scuffs, and scratches.
- Visible tool marks and blemishes: As-machined finishes retain the small tool marks and blemishes from the machining process, which may affect the aesthetic appearance of the parts.
Ultimately, the selection of as-machined finishes for CNC machining should be based on a careful evaluation of the specific project requirements, balancing dimensional tolerances, affordability, and the need for protective coatings. Consulting our team of experts at Precision Machining Pro will ensure the best surface finish choice for your CNC machined parts.
Advantages of As-Machined Finishes | Disadvantages of As-Machined Finishes |
---|---|
Tight dimensional tolerances | Lack of protection |
Affordability | Visible tool marks and blemishes |
Anodizing as a Surface Finish for CNC Machining
In the realm of surface finishes for CNC machining, anodizing stands out as a highly effective and widely used method. Anodizing is an electrochemical process that enhances the natural oxide layer found on CNC machine parts, resulting in a thicker, denser, and more durable surface. This process not only improves the appearance of the parts but also enhances their functional properties, making anodizing a popular choice among manufacturers.
Anodizing is particularly well-suited for aluminum or titanium alloys, as these metals conduct electricity effectively. By subjecting the parts to anodizing, a protective oxide layer is developed through the electrochemical reactions that occur. This layer, now thicker and more robust, enhances the part’s durability and corrosion resistance, prolonging its lifespan in demanding environments.
“Anodizing enhances the natural oxide layer, resulting in a more durable surface.”
Anodizing comes in two primary types: Type II, also known as decorative anodizing, and Type III, which is referred to as hardcoat anodizing. Type II produces coatings that range in thickness from a few micrometers to 25 μm. These coatings are smooth and elegant, providing excellent aesthetic value. On the other hand, Type III anodizing is capable of producing coatings as thick as 125 μm. These hardcoat anodized finishes offer exceptional wear resistance, making them suitable for parts subjected to heavy usage or harsh environments.
Type of Anodizing | Coating Thickness | Properties |
---|---|---|
Type II (Decorative Anodizing) | Up to 25 μm | Smooth and elegant finish |
Type III (Hardcoat Anodizing) | Up to 125 μm | High wear resistance |
Anodizing is valued not only for its durability and corrosion resistance but also for its ability to create aesthetically pleasing surfaces. The range of colors available through anodizing processes allows manufacturers to customize the appearance of their CNC machined parts, matching their intended design or branding preferences.
In summary, anodizing is an electrochemical process that thickens the natural oxide layer on CNC machine parts, resulting in a stronger, longer-lasting surface. With options for both decorative and hardcoat finishes, anodizing offers durability, corrosion resistance, and a wide range of aesthetic possibilities.
Powder Coating for CNC Machined Parts
Precision Machining Pro offers a range of surface finishing options for CNC machined parts, and one of the most effective methods is powder coating. This process involves the application of a dry powder coating using an electrostatic spray gun, followed by curing in an oven. Powder coating provides numerous advantages, including excellent corrosion resistance and impact resistance, making it an ideal choice for various applications.
One of the key benefits of powder coating is its ability to create a strong and durable protective layer on CNC machined parts. The powder is electrostatically charged, allowing it to adhere evenly to the surface. Once cured, the powder forms a tough and wear-resistant finish that can withstand harsh conditions and protect the underlying material.
Unlike traditional spray painting, which uses liquid coatings, powder coating is a dry process. This eliminates the risk of drips, runs, and other imperfections, resulting in a more uniform and high-quality finish. Moreover, multiple layers of powder coating can be applied to achieve the desired thickness, with typical coatings ranging from 30 to 60 microns and, in certain cases, even up to 72 microns.
Another advantage of powder coating is its compatibility with all metals, including steel, aluminum, and alloys. This versatility makes it suitable for a wide range of CNC machined parts, regardless of the material used. Powder coating can also be applied to complex shapes and intricate designs, ensuring consistent coverage and a seamless finish.
Furthermore, powder coating offers superior impact resistance compared to other surface finish options like anodizing. This makes it particularly suitable for parts that may be subjected to mechanical stress, such as automotive components, outdoor equipment, and machinery.
However, it’s important to note that powder coating may yield less dimensional control compared to other finishes. The thickness of the coating can result in slight variations, particularly in tight tolerance areas. Additionally, powder coating is not recommended for small components or internal surfaces where dimensional accuracy is critical.
To summarize, powder coating is a highly effective surface finishing option for CNC machined parts. Its corrosion resistance, impact resistance, and aesthetic appeal make it a popular choice across various industries. When combined with precision machining techniques, powder coating can provide durable and visually appealing finishes that meet the highest standards of quality and performance.
Advantages of Powder Coating for CNC Machined Parts:
- Excellent corrosion resistance
- Superior impact resistance
- Durable and wear-resistant finish
- Uniform and high-quality coating
- Compatible with all metals
Disadvantages of Powder Coating for CNC Machined Parts:
- Potential for less dimensional control
- Not recommended for small components or internal surfaces
When considering the best surface finish for CNC machined parts, it’s crucial to assess the specific requirements of your project. Our team of experts at Precision Machining Pro can help you navigate the various finishing options available, ensuring you achieve the desired functionality and appearance for your CNC machined parts.
Bead Blasting for CNC Machined Parts
At Precision Machining Pro, we offer bead blasting as a surface finishing option for CNC machined parts. Bead blasting is a process that uses pressurized air and glass beads to remove tool marks and imperfections, resulting in a consistent grainy finish. Unlike other surface finishes such as anodizing or powder coating, bead blasting does not add any chemical or mechanical properties to the part. It is purely a visual finish designed to enhance the overall aesthetic appeal of the part.
Bead blasting is an affordable option for those looking to achieve a matte or satin finish on their CNC machined parts. It is a cost-effective alternative to more expensive surface finishes while still providing an attractive result. However, it’s important to note that bead blasting requires skilled operators and manual execution to ensure a high-quality finish. The final appearance of the part depends on the operator’s expertise and the size and grade of the glass beads used in the blasting process.
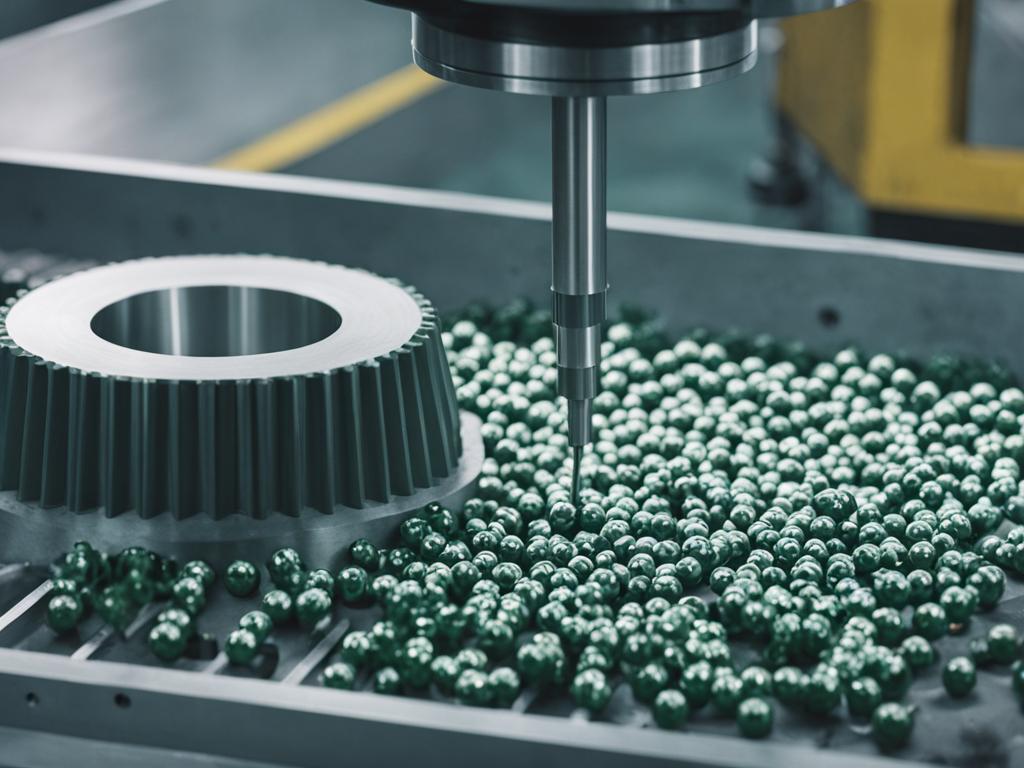
Combining Surface Finishes for CNC Machining
When it comes to surface finishes for CNC machining, sometimes one finish is not enough to achieve the desired results. That’s where the combination of different surface finishes comes into play. By strategically combining finishes, we can enhance both the functionality and aesthetics of CNC machined parts.
A great example of combining surface finishes is using bead blasting to create a specific texture before applying another finish. Bead blasting can help remove tool marks and imperfections, creating a consistent grainy finish that serves as a perfect base for subsequent finishes.
As-machined finishes, while prioritizing dimensional integrity, may not always meet the desired aesthetic requirements. In such cases, protective coatings like anodizing and powder coating can be applied on top of the as-machined finish. These protective coatings not only enhance the appearance of the part but also provide additional durability and corrosion resistance.
On the other hand, if the primary goal is purely aesthetic, mechanical finishes like bead blasting can be used to achieve the desired look. Bead blasting can add a matte or satin finish to the part, purely for aesthetic purposes.
Ultimately, the choice of surface finishes should consider the specific requirements and applications of the CNC machined part. By combining different finishes strategically, we can achieve the perfect balance between functionality and aesthetics.
Benefits of Combining Surface Finishes
The combination of surface finishes in CNC machining offers several benefits. Firstly, it allows us to customize the appearance of a part based on specific design requirements. Whether it’s a smooth and elegant finish or a textured and unique surface, combining finishes gives us the freedom to achieve the desired look.
Secondly, combining finishes can enhance the overall performance of CNC machined parts. Protective coatings like anodizing and powder coating provide added strength, corrosion resistance, and even electrical conductivity. By layering these protective coatings over the as-machined finish, we can ensure the part’s longevity and functionality.
Lastly, combining surface finishes can help optimize manufacturing costs. By strategically selecting the most suitable finishes for each part, we can minimize expenses while still achieving the desired aesthetic and functional outcomes.
Summary
Combining surface finishes in CNC machining opens up a world of possibilities. By carefully selecting and layering finishes, we can achieve the perfect balance between functionality and aesthetics. Whether it’s enhancing the appearance, adding protective coatings, or purely focusing on aesthetic finishes, the choice of surface finishes should always consider the specific requirements and applications of the CNC machined part.
Pre-Surface Finish Processes for CNC Parts
Before applying surface finishes to CNC machined parts, several pre-finishing processes are commonly performed in the industry. These processes ensure that the workpiece is properly prepared and free from any contaminants or defects that could affect the quality of the final surface finish. The main pre-surface finish processes include degreasing, deburring, grinding, and inspection.
Degreasing
Degreasing is a crucial step in the pre-finishing process, especially for parts that have been in contact with oils, lubricants, or other contaminants. It involves the removal of these substances using various solvents or specialized cleaning solutions. Degreasing ensures that the workpiece is clean and free from any residue that could interfere with the adhesion or quality of the surface finish.
Deburring
Deburring is the process of removing sharp edges, burrs, or protrusions from the workpiece. These imperfections can be created during CNC machining and can affect both performance and safety. Deburring is typically done using specialized tools or abrasive methods to smooth out the edges and ensure a uniform surface. By eliminating burrs, the final surface finish can adhere properly, and the part’s functionality and usability can be improved.
Grinding
Grinding is a mechanical pre-finishing process that uses an abrasive wheel to clean the surface of the workpiece. It is particularly useful for removing any remaining tool marks, surface irregularities, or surface contaminants. Grinding helps to achieve a smoother and more uniform surface, which in turn improves the quality of the final surface finish. This process is often performed after deburring to further refine the workpiece’s surface.
Inspection
Inspection is a critical step in the pre-finishing process to ensure that the workpiece meets the required specifications and quality standards. It involves a thorough examination of the part for any defects, such as surface cracks, scratches, or dimensional inaccuracies. Any identified issues are addressed and rectified before proceeding to the surface finishing stage. Inspection helps to ensure that the final surface finish will be applied to a high-quality workpiece.
By carrying out these pre-surface finish processes, CNC machining professionals can ensure that the workpiece is properly prepared for the application of the desired surface finish. Degreasing eliminates contaminants, deburring removes imperfections, grinding improves the surface quality, and inspection identifies and resolves any defects. These processes contribute to achieving the desired surface finish results and help to produce CNC machined parts of superior quality and performance.
Chemical Finishing for CNC Parts
Chemical finishing is a crucial step in the surface treatment of CNC machined parts. This process involves using various chemical techniques to apply coatings that provide both protection and aesthetic appeal. At Precision Machining Pro, we offer a range of chemical finishing options to meet the diverse needs of our clients.
Anodizing
One of the most common chemical finishing methods for CNC parts is anodizing. This electrochemical process creates a protective oxide layer on the surface of the part, enhancing its durability and corrosion resistance. Anodizing is particularly effective for aluminum and titanium alloys, as they have excellent electrical conductivity.
Anodizing can be classified into two types: Type II and Type III. Type II anodizing, also known as decorative anodizing, creates a smooth and elegant coating up to 25 μm thick. On the other hand, Type III anodizing, or hardcoat anodizing, can produce coatings up to 125 μm thick, offering superior wear resistance.
Alodine Coating
Alodine coating, also called chromate conversion coating, is another popular chemical finishing option. It involves applying a chromate layer to the CNC part’s surface, improving its corrosion resistance. Alodine coating is especially beneficial for aluminum and other non-ferrous metals.
Black Oxide Coating
Black oxide coating is a chemical finishing process that forms a dark oxide layer on steel, copper, and other alloys. This coating not only provides corrosion resistance but also gives the part an attractive black appearance. Black oxide coating is commonly used for both functional and decorative purposes.
Electroplating
Electroplating is a chemical finishing technique that involves depositing a thin layer of metal onto the CNC part’s surface. This process enhances the part’s appearance and provides additional protection against corrosion and wear. Electroplating can be performed using a variety of metals, including gold, silver, nickel, and zinc.
Passivation
Passivation is a chemical finishing method primarily used for stainless steel parts. It involves removing impurities from the surface and creating a uniform oxide layer, improving the part’s corrosion resistance and overall surface quality. Passivation ensures that the stainless steel part meets the highest standards of performance and longevity.
Combining different chemical finishing methods can further enhance the properties and appearance of CNC machined parts. At Precision Machining Pro, our experienced team can assist you in selecting the most suitable chemical finishing options for your specific application.
Combining Surface Finishes for CNC Parts
At Precision Machining Pro, we understand that selecting the right surface finish for CNC parts can greatly impact their functionality and aesthetics. In some cases, combining different surface finishes can yield desired results that meet specific requirements. By strategically combining as-machined finishes, chemical finishes, and mechanical finishes, CNC parts can achieve both dimensional integrity and enhanced protection and aesthetics.
As-machined finishes: As-machined finishes are ideal for parts that prioritize dimensional integrity. These finishes offer tight dimensional tolerances, ensuring precise fit and functionality. By themselves, as-machined finishes may lack protection and visual appeal. However, when combined with other surface finishes, they can serve as a solid foundation for achieving desired results.
Chemical finishes: Chemical finishes like anodizing, alodine coating, black oxide coating, and electroplating provide both protection and aesthetic appeal to CNC parts. Anodizing, for example, enhances corrosion resistance and durability by thickening the natural oxide layer on the part’s surface through an electrochemical process. Alodine coating and black oxide coating offer additional corrosion resistance and aesthetic customization options. Electroplating produces a thin metallic layer for improved appearance and wear resistance.
Mechanical finishes: Mechanical finishes, such as bead blasting, can add texture and enhance the overall appearance of CNC parts. Bead blasting utilizes pressurized air and glass beads to remove tool marks and imperfections, resulting in a consistent grainy finish. This mechanical finish is purely for aesthetic purposes and can be combined with other surface finishes to achieve desired textures or visual effects.
When combining surface finishes for CNC parts, it is essential to consider the specific requirements and applications of the parts. Careful planning and coordination between different finishing techniques can lead to optimal results, balancing functionality, protection, and aesthetics. At Precision Machining Pro, our team of experts can provide valuable guidance and expertise in selecting and combining the right surface finishes for your CNC parts.
Considerations for Selecting Surface Finishes for CNC Machining
When it comes to selecting surface finishes for CNC machining, we must carefully consider several factors. Material properties, application requirements, aesthetics, and impact resistance all play a crucial role in determining the best surface finish for a CNC machined part.
The material properties of the part are a key consideration when selecting a surface finish. Factors such as electrical conductivity and susceptibility to corrosion can influence the choice of finish. For example, if the material is highly conductive, anodizing may not be the most suitable option, as it involves the application of an electrochemical process.
Application requirements also come into play. The intended use of the CNC machined part and the environment it will be exposed to should inform the selection of the surface finish. For instance, if the part will be used in a corrosive environment, a finish with enhanced corrosion resistance would be necessary to ensure the longevity of the part.
Aesthetics can also be an important consideration, particularly if the CNC machined part will be visible or used for decorative purposes. Surface finishes like powder coating or bead blasting can enhance the appearance of the part, providing a desired texture or a specific visual effect.
Lastly, impact resistance is another factor to take into account. Some surface finishes offer greater impact resistance than others, which can be crucial depending on the application of the CNC machined part. For instance, if the part is subject to mechanical stress or potential impacts, a finish with high impact resistance would be recommended to prevent damage or deformation.
It is important to evaluate all these factors and match the surface finish with the specific needs of the CNC machined part. By carefully considering material properties, application requirements, aesthetics, and impact resistance, we can select the surface finish that will ensure optimal functionality and performance for the CNC machined part.
The Importance of Consulting Manufacturing Experts
When it comes to selecting the best surface finish for CNC machined parts, consulting manufacturing experts is crucial. At Precision Machining Pro, we understand the importance of surface finish selection in achieving optimal functionality and aesthetics. Our team of experienced professionals has extensive knowledge in precision machining, including surface finishes, and can provide valuable insights and recommendations tailored to your specific project requirements.
By consulting manufacturing experts like us, you can benefit from our deep understanding of different surface finishes and their impacts on the final product. We take into account factors such as material properties, application requirements, and desired aesthetics to guide you in making the right surface finish choices.
We are well-versed in all aspects of manufacturing, from product design to manufacturing at scale. With our expertise, we ensure the selection of the best surface finish for your CNC machined parts, meeting the highest standards of precision and performance.
“Our team of experts at Precision Machining Pro has the knowledge and experience to guide you through the surface finish selection process. We understand the intricacies of precision machining and can help you achieve the desired results for your CNC machined parts.”
Why Consult Manufacturing Experts?
- Expertise: Our team has extensive knowledge and experience in precision machining, allowing us to provide accurate and informed guidance on surface finish selection.
- Industry Insights: We stay up-to-date with the latest advancements and trends in surface finishes for CNC machined parts, ensuring that you have access to the most cutting-edge solutions.
- Customized Recommendations: We understand that each project has unique requirements. By consulting manufacturing experts, you can receive customized recommendations based on your specific needs and goals.
- Optimal Performance: Surface finish selection plays a critical role in achieving optimal performance for CNC machined parts. By consulting with experts, you can ensure that the surface finish aligns with your desired functionality.
At Precision Machining Pro, we are committed to delivering exceptional results and exceeding customer expectations. Consult our manufacturing experts today to discover the best surface finish options for your CNC machined parts.
Benefits of Consulting Manufacturing Experts for Surface Finish Selection |
---|
Access to expertise and knowledge in precision machining |
Customized recommendations based on specific project requirements |
Insights into latest advancements and trends in surface finishes |
Optimal performance through surface finish alignment with functionality goals |
Conclusion
In conclusion, surface finishes play a crucial role in CNC machining by enhancing both the functionality and aesthetics of the parts. When it comes to surface finishes for CNC machining, designers and product managers have several options to choose from. As-machined finishes provide tight dimensional tolerances and affordability, making them the default choice for many applications. However, they may lack protection and have visible tool marks.
Anodizing and powder coating, on the other hand, offer protective coatings that improve durability and corrosion resistance. Anodizing, an electrochemical process, thickens the oxide layer of the part, while powder coating creates a protective layer through the application of dry powder coating. Both options provide not only functionality but also a wide range of colors and finishes.
For purely aesthetic purposes, bead blasting can be applied to achieve a matte or satin finish. Bead blasting removes tool marks and imperfections, giving the part a consistent grainy texture. It is an affordable option but focuses solely on aesthetics and does not provide additional protection.
When selecting surface finishes for CNC machined parts, it is important to consider the specific requirements and applications of the parts. Consulting manufacturing experts can provide valuable guidance in the selection process, ensuring that the chosen surface finish meets the desired standards of precision and performance. By making informed decisions and choosing the right surface finish, designers and product managers can optimize the functionality, durability, and visual appeal of their CNC machined parts.
FAQ
What are the best surface finishes for CNC machining?
The best surface finishes for CNC machining include as-machined finishes, anodizing, powder coating, and bead blasting.
What are as-machined finishes in CNC machining?
As-machined finishes are the default option in CNC machining, providing tight dimensional tolerances and affordability. They have visible tool marks and lack protection.
How does anodizing work as a surface finish for CNC machining?
Anodizing is an electrochemical process that thickens the natural oxide layer on CNC machine parts, providing durability and corrosion resistance.
What is powder coating and how does it work for CNC machined parts?
Powder coating is a process where a dry powder coating is applied to CNC machined parts using an electrostatic spray gun and then cured in an oven. It creates a strong and aesthetically pleasing protective layer on the part.
What is bead blasting and what is it used for in CNC machining?
Bead blasting is a process that uses pressurized air and glass beads to remove tool marks and imperfections, creating a consistent grainy finish on CNC machined parts.
Can different surface finishes be combined in CNC machining?
Yes, different surface finishes can be combined in CNC machining to achieve desired results. For example, bead blasting can be used to create a specific texture before applying another finish.
What are the pre-surface finish processes commonly used for CNC parts?
Pre-surface finish processes commonly used for CNC parts include degreasing, deburring, grinding, and inspection to remove contaminants, sharp edges, and improve surface quality.
What are the chemical finishing options for CNC parts?
Chemical finishing options for CNC parts include anodizing, alodine coating, black oxide coating, electroplating, and passivation to provide protection and enhance surface quality and appearance.
Is it possible to combine different surface finishes for CNC parts?
Yes, it is possible to combine different surface finishes for CNC parts to achieve desired functionality and appearance.
What should be considered when selecting surface finishes for CNC machining?
When selecting surface finishes for CNC machining, factors such as material properties, application requirements, and aesthetics should be taken into account.
Why is it important to consult manufacturing experts when selecting surface finishes for CNC parts?
Consulting manufacturing experts is important when selecting surface finishes for CNC parts because they have extensive knowledge and experience in precision machining and can provide valuable guidance based on specific project requirements.
Source Links
- https://sybridge.com/cnc-finishes/
- https://www.americanmicroinc.com/resources/surface-finishes-cnc-machining/
- https://www.rapiddirect.com/knowledge-base/surface-finishes-for-cnc-machining