When it comes to CNC machining, selecting the right materials selection is crucial for cost-effectiveness. The choice of material can significantly impact the overall cost of the production process. Factors such as material costs, varying machining requirements, and recyclability all play a role in determining CNC machining costs. By properly planning and considering the specific needs of your product, equipment workflows, and potential future changes, you can find the ideal CNC machining material that strikes the perfect balance between cost and quality.
- Choosing the right material is essential for cost optimization in CNC machining.
- Factors such as material costs and machining requirements impact CNC machining costs.
- Considering product needs, equipment, and workflows can aid in finding the most cost-effective material.
- Proper planning and design modifications can help reduce CNC machining costs.
- Understanding the factors that contribute to CNC machining costs is vital for calculating and reducing expenses.
Factors Impacting CNC Machining Costs
When it comes to CNC machining, several factors play a significant role in determining the overall costs. By understanding and addressing these factors, you can effectively reduce CNC machining costs and make the process more affordable and efficient for your business.
Machining Time and Start-up Costs
The amount of time it takes to complete a machining project directly impacts the cost. The longer the machining time, the higher the costs will be. Additionally, start-up costs, which include CAD file preparation and process planning, can be a substantial portion of the overall cost, particularly for small-volume productions.
Material Costs
The choice of material has a significant impact on CNC machining costs. Some materials may be more expensive than others, which can significantly increase the overall cost of production. By selecting affordable CNC machining materials without compromising on quality, you can effectively reduce costs while maintaining the desired outcomes.
Other Manufacturing Costs
In addition to material costs, there are other manufacturing costs to consider. These costs may include special tooling requirements, closer quality control, and additional processing steps. Each of these factors increases both the machining time and the total cost. By carefully evaluating and minimizing these additional costs, you can optimize the manufacturing process and reduce CNC machining expenses.
Material Finish
The desired finish of the CNC machining product can also influence costs. Complex finishes or tight tolerances may require additional time and resources, leading to increased expenses. By considering the specific requirements and evaluating the necessary finish, you can make informed decisions that help in cost reduction.
Reducing CNC machining costs is a multi-faceted process that involves considering machining time, start-up costs, material costs, other manufacturing costs, and material finish. By addressing each of these factors and optimizing your approach, you can achieve cost-effective CNC machining services without compromising on quality.
To further illustrate the impact of these factors on CNC machining costs, let’s take a look at an example table:
Factors | Impact on Cost |
---|---|
Machining Time | Directly proportional to cost – longer machining time means higher costs |
Start-up Costs | The choice of material can significantly impact the overall cost |
Material Costs | Choice of material can significantly impact the overall cost |
Other Manufacturing Costs | Special tooling requirements and additional processing steps increase costs |
Material Finish | Complex finishes or tight tolerances may require additional resources |
This table demonstrates how each factor affects CNC machining costs, providing valuable insights into cost reduction strategies.
CNC Machine Costs and Types
When it comes to CNC machining, the type of machine used can have a significant impact on costs. Understanding these costs can help you make informed decisions and optimize your CNC machining process.
There are two main types of CNC machines: three-axis machines and five-axis machines. Three-axis machines are more standard and typically cost less per hour, making them a popular choice for many machining projects. These machines operate using three axes of motion: X, Y, and Z, allowing for precise and accurate machining.
On the other hand, five-axis machines offer more complex capabilities and greater flexibility. These machines can move across five axes of motion, adding rotation and tilt to the three axes of the three-axis machine. While five-axis machines offer more versatility and can handle more complex parts, they generally come with a higher cost per hour of operation.
Image:
When selecting a machine for your CNC machining needs, it’s essential to weigh the costs and benefits of each type. Consider factors such as the complexity of your parts, the required precision, and your budget. If your project can be accomplished using a three-axis machine, it may be a more cost-effective option. However, if your parts require complex geometries or intricate designs, a five-axis machine may be worth the additional investment.
To further illustrate the differences between three-axis and five-axis machines, let’s take a closer look at their respective costs:
Type of CNC Machine | Cost per Hour (approx.) |
---|---|
Three-Axis Machine | $X |
Five-Axis Machine | $Y |
These average cost-per-hour values are provided as a general guideline and can vary depending on various factors such as machine capabilities, geographic location, and specific project requirements.
By understanding the costs associated with different types of CNC machines, you can make informed decisions that align with your budget and project requirements. Whether you choose a cost-effective three-axis machine or invest in the versatility of a five-axis machine, optimizing your CNC machine costs plays a crucial role in achieving a successful and profitable machining process.
Tips for Reducing CNC Machining Costs
When it comes to CNC machining, cost-effectiveness is always a top priority. By implementing a few design modifications, you can optimize the machining process and reduce costs. Here are some valuable tips for reducing CNC machining costs:
- Use rounded internal corners: Sharp internal corners can increase machining time and costs. By incorporating rounded internal corners, you can streamline the machining process and minimize material waste.
- Limit the depth of cavities: Deep cavities increase the complexity of machining and require additional time and resources. To reduce costs, consider limiting the depth of cavities whenever possible.
- Increase the thickness of thin walls: Thin walls can be more challenging to machine accurately, leading to potential errors and rework. By increasing the thickness of thin walls, you can improve the machinability and reduce costs.
- Limit the length of threads: Long threads require more machining time and increase the risk of tool breakage. To optimize the process, it is recommended to limit the length of threads.
- Use standard hole sizes: Custom hole sizes often require special tooling, resulting in increased costs. By sticking to standard hole sizes, you can minimize tooling expenses and improve cost-effectiveness.
- Specify tolerances only when necessary: Tight tolerances may require additional machining operations, leading to higher costs. Specify tolerances only when they are essential to the functionality of the part.
- Minimize the number of machine setups: Each machine setup adds to the overall machining time and costs. By minimizing the number of setups, you can optimize the process and reduce expenses.
- Avoid small features with high aspect ratios: Small features with high aspect ratios can be challenging to machine accurately, increasing the risk of errors and delays. Avoiding such features can help streamline the process and reduce costs.
- Remove text and lettering: Engraving text and lettering on a part requires additional machining operations. If possible, consider removing unnecessary text and lettering to lower costs.
By implementing these tips, you can effectively reduce CNC machining costs while maintaining product quality and integrity.
Calculating CNC Machining Costs
Understanding the factors that contribute to CNC machining costs is essential for calculating and reducing expenses. By analyzing key variables such as machining time, start-up costs, material costs, and other manufacturing expenses, you can gain valuable insights into the cost structure of a CNC machining project.
One of the primary factors impacting the cost is the length of time required to complete the project. The longer it takes to machine a part, the higher the overall cost will be. Efficiently optimizing the machining process can help reduce the time spent on each part, resulting in significant cost savings.
Another key cost factor is start-up costs, which cover CAD file preparation and process planning. Particularly for small volume productions, start-up costs can make up a substantial portion of the overall expenses. Streamlining these processes and implementing efficient workflows can contribute to cost reduction.
Material costs are also crucial in calculating CNC machining expenses. The choice of material not only affects the cost but also impacts the machinability and overall production efficiency. Selecting cost-effective materials based on the specific requirements of your project can help optimize the final cost without compromising quality.
Other manufacturing costs, such as tooling, quality control, and additional processing steps, can further contribute to CNC machining expenses. Analyzing these costs and finding opportunities to streamline the manufacturing process can help minimize additional expenses and improve cost-effectiveness.
By thoroughly considering these factors and their impact on CNC machining costs, you can calculate the total expenses accurately. This knowledge enables you to make informed decisions to reduce costs and optimize the overall production process.
Calculating CNC Machining Costs Example:
Cost Factor | Calculation |
---|---|
Machining Time | Number of parts x Time per part x Machine hourly rate |
Start-up Costs | Cost of CAD file preparation + Process planning costs |
Material Costs | Total material volume x Material cost per unit volume |
Other Manufacturing Costs | Tooling costs + Quality control costs + Additional processing costs |
By plugging in the specific values for each cost factor, you can accurately calculate the overall CNC machining costs for your project.
Having insights into these calculations simplifies the decision-making process, allowing you to identify areas where cost reduction is possible. By optimizing efficiency, selecting cost-effective materials, and streamlining workflows, you can successfully reduce CNC machining costs while maintaining quality standards.
Machining Time and Start-up Costs
When it comes to CNC machining costs, two factors that significantly impact the overall expense are machining time and start-up costs.
Machining time refers to the duration it takes to machine a part. The longer it takes to complete the machining process, the more expensive it becomes. Time is money in the CNC machining world, with every minute adding up to the final cost. Optimizing machining time by streamlining processes and reducing unnecessary steps can help in reducing costs.
Start-up costs are another important aspect to consider. These costs encompass the preparation of CAD files and the planning of machining processes. For small-volume productions, start-up costs can account for a considerable portion of the overall expenditure. Proper planning and efficient utilization of resources can help minimize start-up expenses and improve cost-effectiveness.
By carefully evaluating machining time and start-up costs, businesses can optimize their production processes and achieve cost savings. Implementing efficient workflows, utilizing advanced machining techniques, and employing experienced operators can all contribute to reducing CNC machining costs.
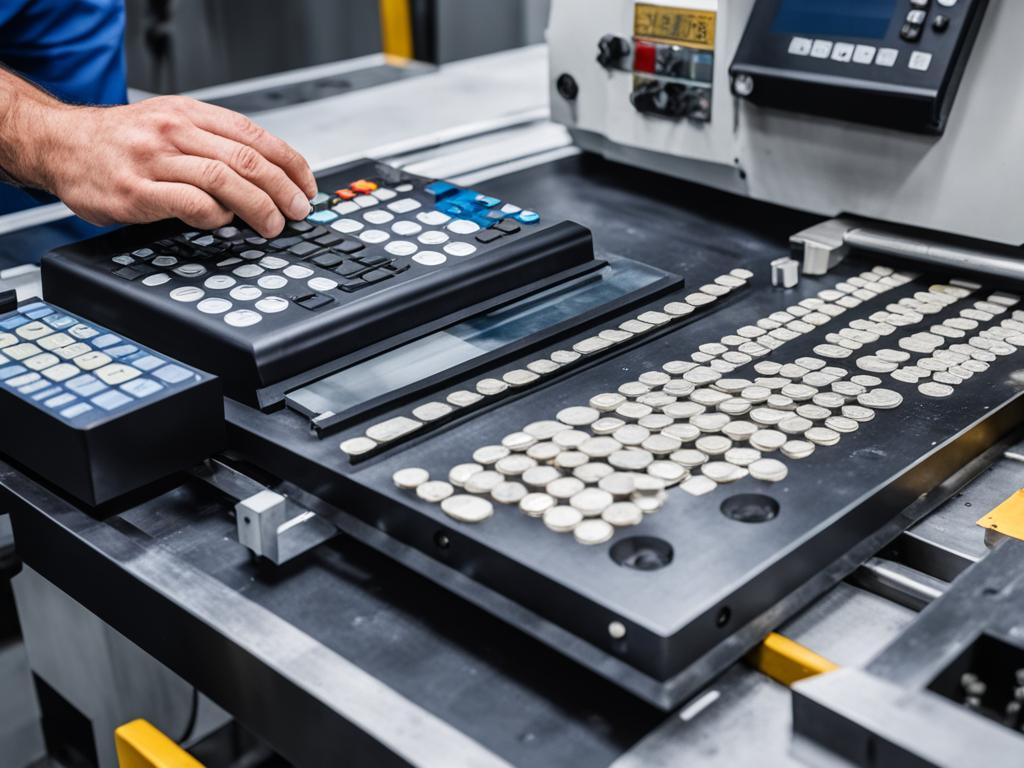
Material Costs and Other Manufacturing Costs
When it comes to CNC machining costs, material costs, and other manufacturing expenses play a significant role. The price of the raw material and its machinability can greatly impact the overall cost of your project. Additionally, specific product requirements may necessitate special tooling, closer quality control, and additional processing steps, all of which can increase machining time and cost.
It is crucial to carefully consider material costs and other manufacturing expenses to find the most cost-effective solution for your CNC machining needs. By selecting affordable CNC machining materials and optimizing the machining process, you can reduce costs without compromising on quality.
Reducing material costs starts with conducting a thorough CNC machining material price analysis. By comparing prices from different suppliers and evaluating their material quality, you can make informed decisions that align with your budget and project requirements. Keep in mind that while lower-cost materials may seem enticing, they may have drawbacks in terms of machinability or overall performance.
In addition to material costs, it’s important to account for other manufacturing expenses. Depending on your project’s complexity and specific requirements, you may incur costs for special tooling, quality control measures, and additional processing steps. By carefully considering these factors and optimizing the machining process, you can effectively reduce CNC machining costs.
Optimizing material selection and understanding the impact of various manufacturing costs will not only help you save money but also ensure that your CNC machining projects are completed efficiently and to your satisfaction.
Comparison of Material Costs
Material | Price per Unit | Machinability |
---|---|---|
Aluminum | $X | High |
Stainless Steel | $Y | Medium |
Titanium | $Z | Low |
Note: The prices mentioned above are indicative and may vary based on market conditions and suppliers.
By carefully analyzing material costs and selecting cost-effective CNC machining materials, you can significantly reduce your overall expenses while still achieving high-quality results.
Material Selection and Cost Optimization
When it comes to CNC machining, selecting the right material is crucial for cost optimization. The properties of the material, such as hardness, thermal conductivity, and recyclability, have a direct impact on the machining process and overall costs. By carefully considering your product needs, equipment workflows, and future changes, you can find the most cost-effective material for CNC machining while ensuring quality.
Choosing the right material starts with understanding its properties and how they align with your specific project requirements. For example, certain materials may offer higher hardness, making them more suitable for applications requiring increased durability. Others may have better thermal conductivity, allowing for efficient heat dissipation. Taking these factors into account helps optimize the machining process and minimize costs.
Additionally, considering your production environment and workflow is essential for cost optimization. By selecting a material that aligns with your existing equipment, you can streamline the machining process and reduce the need for additional investments. Furthermore, anticipating future changes, such as scaling up production or introducing new product variants, can guide you toward materials that offer flexibility while keeping costs in check.
Examples of most used materials selections.
As a guide here are some of the most popular materials used for CNC machined parts.
- Alloy Steel
- Aluminum
- Brass
- Copper
- Plastics
- Stainless Steel
- Steel
- Titanium
- Tungsten
Each of these materials could have hardness grades and different compositions.
One crucial aspect of material selection for cost optimization is the recyclability of the chosen material. Opting for materials that can be easily recycled and reused not only reduces waste but also provides potential cost savings in the long run. Recycling compatible materials reduces the dependence on virgin materials, which can be more expensive and have a negative impact on the environment.
To illustrate the impact of material selection on cost optimization, consider the following example:
Material | Hardness (HRC) | Machining Time (hours) | Cost ($) |
---|---|---|---|
Material A | 50 | 2 | 100 |
Material B | 40 | 3 | 120 |
Material C | 55 | 1.5 | 90 |
In this example, Material C offers the highest hardness (55 HRC) but requires the least machining time (1.5 hours) and has the lowest cost ($90). By selecting Material C, you can optimize costs without compromising on the desired hardness.
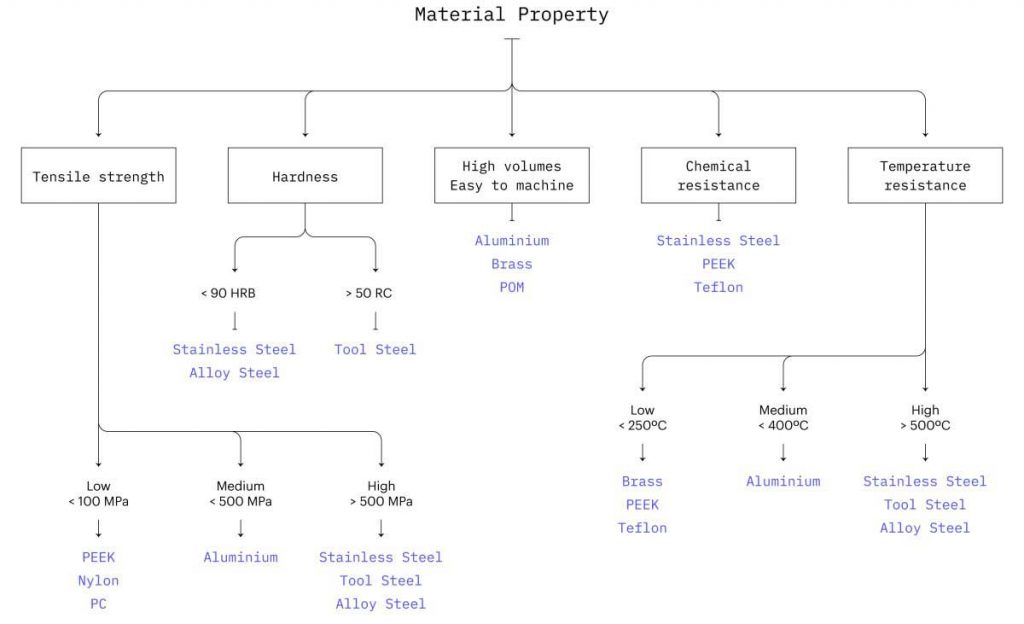
By carefully considering material properties, production needs, and recyclability, you can make informed decisions that optimize material selection for CNC machining, reducing costs while maintaining quality.
Design Modifications for Cost Reduction
When it comes to optimizing CNC machining costs, design modifications can make a significant impact. By incorporating specific design considerations, you can streamline the machining process and reduce expenses. Here are some strategies to help you achieve more cost-effective CNC machining:
- Designing with rounded internal corners: By avoiding sharp corners, you can minimize the complexity of the machining process, resulting in reduced costs.
- Limiting the depth of cavities: Shallow cavities are easier to machine and require less time and resources, leading to cost savings.
- Increasing the thickness of thin walls: Thicker walls offer better stability during machining, reducing the risk of errors and potential rework, which can drive up costs.
- Using standard hole sizes: Standard hole sizes simplify the machining process, as they can be efficiently produced using readily available tools, helping to lower costs.
By implementing these design modifications, you can optimize the CNC machining process and achieve cost reduction without compromising product quality.
“Effective design modifications can greatly contribute to cost reduction in CNC machining. By focusing on simplifying the machining process through rounded internal corners, limited cavity depth, increased wall thickness, and the use of standard hole sizes, businesses can unlock significant cost savings without sacrificing precision or quality.”- Industry Expert
The Impact of Tolerances and Finishes
Tight tolerances and complex finishes can significantly impact CNC machining costs. When specifying tolerances for your projects, it’s important to carefully consider their necessity. Tighter tolerances require more precise machining and result in increased costs. By only specifying tolerances when necessary, you can reduce machining time and improve cost-effectiveness.
In terms of finishes, opting for standard finishes can help reduce costs. Complex finishes require additional steps and specialized equipment, which adds to the overall expense. Choosing standard finishes that still meet your quality requirements can help optimize the machining process and save you money.
Another key factor to consider when optimizing CNC machining costs is the machinability of the material. Some materials are more difficult to machine than others, which can increase machining time and costs. By selecting materials that are known for their machinability, you can streamline the process and achieve more cost-effective results.
Insert relevant H3 if applicable
Tolerance Level | Impact on Costs |
---|---|
Tight Tolerances | Higher machining precision, increased costs |
Loose Tolerances | Less machining precision, reduced costs |
By balancing tolerances and finishes with cost considerations, you can optimize material selection for CNC machining and achieve greater cost-effectiveness without compromising on quality.
Finish Type | Impact on Costs |
---|---|
Standard Finish | Cost-effective, meets quality requirements |
Complex Finish | Additional steps, specialized equipment, higher costs |
Streamlining Machine Setups and Complex Parts
Streamlining machine setups and handling complex parts are effective strategies for reducing CNC machining costs. By optimizing the machining process and minimizing setup time, you can achieve cost-efficiency without compromising on quality.
Designing parts that can be machined in fewer setups is a key factor in reducing costs. When possible, consolidate multiple machining operations into a single setup, eliminating the need for repeated machine adjustments and reducing production time. Additionally, utilizing simple geometries can streamline the machining process, as complex shapes often require more time and resources to manufacture.
Avoiding small features with high aspect ratios is another way to optimize the machining process. These features can be challenging to machine accurately and efficiently, leading to increased costs. By redesigning parts to eliminate or simplify these elements, you can minimize machining time and improve cost-efficiency.
“Simplifying the machining process can lead to significant cost reductions while maintaining quality.”
Here is an example of how streamlining machine setups and simplifying part design can reduce CNC machining costs:
Scenario | Machine Setups | Machining Time | Cost |
---|---|---|---|
Original Design | 3 | 6 hours | $500 |
Optimized Design | 1 | 3 hours | $250 |
In the original design, the complex part required three machine setups, resulting in a higher machining time and cost. However, after redesigning the part to simplify its geometry and consolidate machining operations, the number of setups was reduced to one, significantly reducing machining time and cost.
By streamlining machine setups and optimizing part design, you can achieve cost-efficient CNC machining. These strategies not only reduce production costs but also improve productivity, allowing you to deliver high-quality products on time and within budget.
Final Thoughts
The selection of materials plays a pivotal role in optimizing CNC machining costs. By carefully considering factors such as machining time, start-up costs, material costs, and design modifications, businesses can significantly reduce expenses without compromising on quality. To achieve cost-effective CNC machining, it is essential to make well-informed decisions tailored to your specific needs and equipment.
By analyzing the machining time and start-up costs associated with your project, you can identify areas that require optimization. Additionally, carefully evaluating material costs and exploring cost-effective CNC machining materials can result in substantial savings. Don’t overlook the potential impact of design modifications in reducing costs. Simple changes such as rounded internal corners, limited cavity depth, increased thickness of thin walls, and standardized hole sizes can all contribute to a more efficient and affordable machining process.
In conclusion, the key to reducing CNC machining costs lies in strategic material selection and thoughtful design considerations. By understanding the various cost drivers and making informed choices, you can optimize the material selection process for CNC machining. This will ultimately position your business for cost-effective production while maintaining the desired quality standards.
FAQ
How does material selection impact CNC machining costs?
Material selection is crucial for cost-effectiveness in CNC machining. Different materials have varying machinability and costs, which can impact the overall cost of the project. Choosing the right material based on product needs, equipment and workflows, and future changes can help find a cost-effective solution.
What factors affect CNC machining costs?
Several factors impact CNC machining costs, including machining time, start-up costs, material costs, and other manufacturing costs. Machining time and start-up costs are key cost drivers, while material selection and product requirements also influence costs.
How do CNC machine costs vary?
CNC machine costs vary based on the type of machine used. Three-axis machines are more standard and typically cost less per hour, while five-axis machines are more complex and cost more. Understanding the costs associated with different types of machines can help in selecting the most cost-effective option for CNC machining.
What are some tips for reducing CNC machining costs?
To reduce CNC machining costs, design modifications can be made, such as using rounded internal corners, limiting the depth of cavities, increasing the thickness of thin walls, and specifying tolerances only when necessary. Streamlining machine setups, avoiding small features with high aspect ratios, and removing unnecessary text and lettering can also help optimize the machining process and reduce costs.
How can I calculate CNC machining costs?
CNC machining costs are determined by factors such as machining time, start-up costs, material costs, and other manufacturing costs. The length of time required to complete the project and the specific machine used impact the cost. Understanding how these factors contribute to the overall cost can help in calculating and reducing CNC machining costs.