Welcome to Precision Machining Pro, where we specialize in delivering high-quality CNC machining solutions. In this article, we will explore the crucial relationship between CNC tolerances and manufacturing prices. As precision is essential in CNC machining, the tolerances specified in the design have a significant impact on the cost of production.
CNC tolerances determine the allowable extent for deviations in part dimensions. These tolerances affect various aspects of the manufacturing process, from material selection to inspection requirements. Tighter tolerances often result in higher production costs due to increased scrap, the need for specialized tools and equipment, additional testing and inspection, and the requirement for additional machining processes. On the other hand, looser tolerances may result in lower costs but sacrifice precision and quality.
Key Takeaways:
- Tighter tolerances generally result in higher production costs due to increased scrap, specialized tools, and additional processes.
- The choice of material for CNC machining can greatly impact the achievable tolerance. Softer materials can be more difficult to maintain precise tolerances.
- The design of CNC parts plays a crucial role in controlling tolerances and ensuring part quality. Factors such as part geometry and overall dimensions impact achievable tolerances.
- Tighter tolerances require more advanced measurement equipment and inspection techniques, leading to higher inspection costs.
- To optimize costs, it is essential to carefully consider the tolerance requirements, choose cost-effective materials, and utilize cost-saving design approaches.
Tolerance Levels and Their Impact on Production Costs
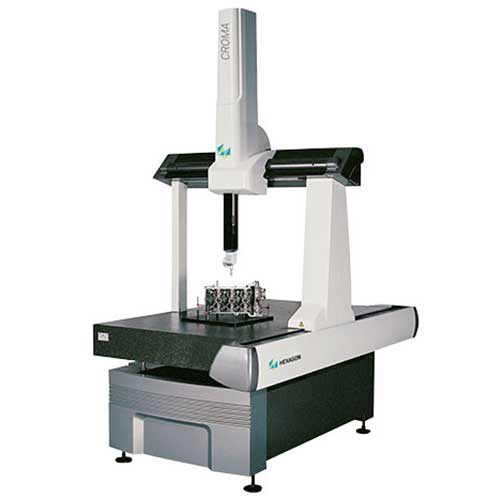
CNCxpress makes parts for CROMA-3d-Measuring-equipment
When it comes to CNC machining, tolerance levels have a direct impact on production costs. The choice of tolerance can significantly affect various aspects of the manufacturing process, leading to cost variations. Let’s explore how tolerance levels influence production costs and what factors should be considered.
Tighter tolerances often result in increased machining turnaround time. Achieving tighter part tolerances requires more precision and meticulousness, which can slow down the production process. As a result, additional time is needed to ensure the desired accuracy, leading to higher production costs.
Moreover, tighter tolerances may require the use of specialized tooling. These tools are specifically designed to achieve the required precision but often come at a higher cost. The expense associated with specialized tooling can contribute to higher production costs.
Additionally, achieving tighter tolerances typically involves expensive tests and inspections. Thorough inspection is required to ensure that the parts meet the specified tolerances. The use of advanced measurement equipment and inspection techniques adds to the overall production costs.
Furthermore, tighter tolerances may necessitate additional machining processes to achieve the desired surface finish. These extra processes, such as grinding or polishing, can add complexity and cost to the production workflow.
The cost of design and production can also be significantly higher when tighter tolerances are required. Adhering to tighter tolerances often demands meticulous design considerations, which can increase design complexity and development costs.
Table: Comparison of Standard Tolerance Levels and Tighter Part Tolerances
Tolerance Levels | Production Costs |
---|---|
Standard Tolerance Levels | Lower |
Tighter Part Tolerances | Higher |
It is important to carefully consider the tolerance requirements for CNC parts. While tighter tolerances may be necessary in certain applications, it is essential to assess the cost implications. Balancing precision and cost-effectiveness is crucial in achieving optimal manufacturing outcomes.
“Tighter tolerances often lead to increased machining turnaround time, the use of specialized and expensive tooling, the need for expensive testing and inspection processes, and the requirement for additional machining processes to achieve the desired surface finish.”
The Influence of Tolerances on the Manufacturing Process
In the manufacturing process of CNC parts, tolerance requirements play a crucial role in determining the choice of machining operations and procedures. Different tolerance levels may necessitate distinct manufacturing approaches, resulting in variations in lead times, production costs, and overall manufacturing precision.
When determining the appropriate tolerance requirements for CNC parts, it is important to consider the specific characteristics of the manufacturing process. The choice of CNC machine is influenced by the tolerances needed, as different machines may have varying tolerance capabilities. Selecting the right machine ensures that the desired tolerance levels can be achieved efficiently and effectively.
In some cases, achieving tight tolerances may require additional machining operations beyond the primary machining process. These additional operations may be necessary to produce small or fine finishing features that meet the specified tolerance requirements. Operations such as grinding or lapping may be employed to meet even tighter tolerance standards, ensuring the desired surface roughness and characteristics.
The complexity of the part design and the overall dimensions also contribute to the manufacturing process and the control of tight tolerances. Design features such as intricate geometries, sharp internal corners, and narrow regions may require special considerations and machining techniques to maintain the desired tolerances. This attention to detail ensures the necessary manufacturing precision to produce high-quality CNC parts.
Case Study: Precision Machining Pro
“At Precision Machining Pro, we understand the criticality of tolerances in the manufacturing process. Our experts meticulously analyze tolerance requirements to optimize the choice of machining operations, CNC machines, and additional machining procedures. By leveraging advanced technology and our extensive expertise, we deliver CNC parts with precise tolerances, exceptional manufacturing precision, and minimized production costs.”
When it comes to CNC manufacturing, acknowledging the influence of tolerances on the manufacturing process is paramount. By carefully considering tolerance requirements, selecting appropriate machining operations, utilizing the right CNC machines, and implementing additional machining procedures, manufacturers can achieve optimal manufacturing precision while meeting cost and time constraints.
Material Considerations for Tolerances
When it comes to CNC machining, the choice of material plays a crucial role in determining the achievable tolerance levels. Different materials possess unique qualities that directly impact their compatibility with specific tolerance requirements.
Softer materials, such as thermosets and thermoplastics, may pose challenges in maintaining precise tolerances. During the machining process, these materials have a tendency to flex, making it difficult to achieve the desired dimensional accuracy.
Non-metal materials, including plastics, can also experience thermal stability issues. The heat generated during machining can cause deformation, leading to variations in tolerances.
On the other hand, materials with high carbon content, like carbon steel and titanium, can be more abrasive. Due to their hardness, achieving specific tolerance requirements can be more challenging.
Conversely, harder materials, such as aluminum, stainless steel, brass, and copper, are generally easier to process and achieve precise tolerances. The enhanced machinability of these materials facilitates the alteration of dimensions during the machining process with greater ease.
When determining tolerance requirements for CNC parts, it is important to carefully consider the material properties. Material selection plays a vital role in ensuring successful machining processes that meet the desired tolerance levels.
Design Factors Impacting Tolerances
The design of CNC parts plays a crucial role in controlling tolerances and ensuring part quality. Various factors must be considered to achieve the desired tolerance levels while maintaining optimal production costs and customer satisfaction.
Part Geometry
The geometry of the part directly affects the achievable tolerances. Features with sharp internal corners or narrow regions may require special considerations to achieve the desired tolerance. Complex geometries may also introduce challenges in maintaining tight tolerances throughout the part. Therefore, careful analysis and adjustments in the design phase are essential to optimize tolerances and minimize production costs.
Overall Dimensions
The overall dimensions of the part have a significant impact on tolerance control. Thick walls, for example, may experience varying shrink rates within different sections, making it challenging to maintain precise tolerances throughout the part. By carefully considering the overall dimensions during the design phase, consistent tight tolerances can be achieved.
Wall Thickness
Wall thickness is another critical design factor that affects tolerances. Thick walls may require additional machining processes or specialized tooling to achieve the desired tolerance levels. Therefore, it is important to analyze the wall thickness and make necessary adjustments to ensure optimal part quality and cost-effectiveness.
Shrink Rates
Shrink rates can vary depending on the material used, which can impact the achievable tolerances. Different materials have distinct shrinkage characteristics during the cooling process, and these variations can affect the final dimensions of the part. Understanding the shrink rates associated with specific materials is crucial in designing CNC parts with precise tolerances.
Part Quality and Customer Satisfaction
The design factors impacting tolerances ultimately contribute to part quality and customer satisfaction. By controlling tolerances through proper design considerations, manufacturers can ensure that the finished parts meet the required specifications and customer expectations. Consistent, high-quality parts not only enhance customer satisfaction but also help minimize expenses associated with rework or rejected parts.
Expenses and Tolerance Control
Tolerance control is closely tied to expenses in CNC machining. Tighter tolerances may require additional machining processes, specialized tooling, or post-processing steps, resulting in increased production costs. Design factors such as part geometry, overall dimensions, and wall thickness should be carefully evaluated to strike a balance between tolerance control and cost-effectiveness.
Part Inspection
Design factors impact the complexity of part inspection. Tighter tolerances may necessitate more rigorous, time-consuming inspection processes to ensure compliance. By considering inspection requirements during the design phase, manufacturers can optimize tolerances while minimizing the time and cost associated with part inspection.
Our Precision Machining Pro team understands the criticality of design factors in achieving tight tolerances for CNC parts. By leveraging our expertise and state-of-the-art equipment, we can help you optimize part designs for precise tolerances while ensuring cost-effectiveness and high-quality results.
Impact of Tolerances on Parts Inspection
Tolerances play a critical role in the inspection of CNC parts, significantly influencing the processes and costs involved. When tighter tolerances are required, the inspection becomes more intricate, demanding advanced measurement equipment and sophisticated techniques to ensure accuracy.
Inspecting parts with tighter tolerances can be time-consuming and labor-intensive. The complexity of verification increases, and deviations such as chatter marks become harder to detect and analyze. It is essential to invest in high-quality inspection tools and techniques to meet the stringent requirements.
Furthermore, the inspection of tighter tolerances can result in higher part production costs. The additional time and effort required to inspect these parts contribute to increased labor costs and overall manufacturing expenses.
Considering the cost implications of tolerance inspection is vital when determining the acceptable tolerance levels for CNC parts. A balance must be struck between achieving the desired precision and controlling production costs.
Inspection Technique | Features | Benefits |
---|---|---|
Coordinate Measuring Machine (CMM) | – Measures complex geometries accurately – Allows inspection of multiple features simultaneously | – High precision and repeatability – Efficient and automated process |
Optical Metrology | – Non-contact measurement – Suitable for delicate or fragile parts | – Fast and accurate measurements – 3D scanning capabilities |
X-ray Inspection | – Detects internal defects and inconsistencies – Suitable for complex and intricate parts | – Non-destructive testing – Reveals hidden features or structures |
Surface Profilometry | – Measures surface roughness and texture – Evaluates wear, corrosion, and coating quality | – Provides detailed surface analysis – Essential for achieving specific finish requirements |
By investing in appropriate inspection techniques and implementing quality control measures, manufacturers can ensure that the tolerances are met, maintaining the desired precision and minimizing the risk of costly errors. Comprehensive inspection practices are crucial for delivering high-quality CNC parts that meet customer expectations and industry standards.
Cost Optimization Strategies for CNC Tolerances
To optimize costs in CNC machining projects, we employ various strategies that consider material costs, part complexity, post-processing requirements, CNC machine setups, fixturing, specialized tools, and optimized toolpaths. By carefully analyzing these factors and making informed decisions, we can achieve cost-effective manufacturing without compromising quality and precision.
Material Costs
Material selection plays a crucial role in determining project costs. Some materials are more expensive than others, and opting for cost-effective options can significantly impact CNC machining expenses. By considering the specific requirements of the project alongside the cost of different materials, we can strike a balance between quality and affordability.
Part Complexity
The complexity of a part directly affects manufacturing costs. Intricate designs often require multiple setups on CNC machines, resulting in increased project costs. By carefully analyzing part complexity and exploring design alternatives, we can simplify the manufacturing process and minimize expenses without compromising functionality.
Post-Processing Requirements
Post-processing, such as finishing or surface treatment, can add significant costs to CNC machining projects. By analyzing the desired surface finish and evaluating alternative methods, we can identify cost-effective approaches that meet the necessary quality standards. This includes considering options such as eliminating or reducing post-processing requirements while maintaining the desired aesthetics and functionality.
CNC Machine Setups
Multiple setups on CNC machines can significantly impact project costs. Each setup requires machine resetting, tool recalibration, and, in some cases, the design and production of custom fixtures. Careful planning and optimization of the machining process can minimize the need for multiple setups, reducing manufacturing time and associated costs.
Specialized Tools and Optimized Toolpaths
In some cases, specialized tools may be necessary to achieve tight tolerances or specific part features. However, these tools can be costly. By analyzing the design requirements and exploring alternative tooling options, we can minimize expenses without compromising on precision. Additionally, optimized toolpaths can reduce machining time and minimize tool wear, further optimizing costs.
Overall Production Volume
Considering the overall production volume is crucial in cost optimization. Ordering more parts at a time can often result in lower costs per part. By analyzing the production requirements and projected demand, we can optimize the order quantity to capitalize on economies of scale.
Optimizing CNC machining costs requires a comprehensive understanding of various factors and their interplay. By employing effective cost optimization strategies and making informed decisions at every stage of the process, we can deliver high-quality CNC machined parts while minimizing expenses.
Table:
Cost Optimization Strategies for CNC Tolerances |
---|
Consider material costs |
Account for part complexity |
Evaluate post-processing requirements |
Minimize multiple CNC machine setups |
Optimize tooling and toolpaths |
Consider overall production volume |
Material Selection for Cost-Effective CNC Machining
When it comes to CNC machining, the selection of materials is crucial in determining project costs. Several factors, including material strength, machinability, cost, and availability, should be carefully considered to achieve cost-effective manufacturing. Let’s explore these factors in detail.
Material Strength and Machinability
The strength of the material affects its suitability for CNC machining. While exotic materials may offer exceptional properties, they tend to be more expensive. In contrast, common materials such as aluminum and low carbon steel provide a balance between strength and affordability. These materials are not only cost-effective but also easier and faster to machine, reducing overall project costs. Opting for materials with good machinability not only saves time but also increases productivity and efficiency.
Material Cost and Availability
Material cost is a significant consideration in CNC machining. Metals generally tend to be more expensive than plastics. By choosing materials like aluminum, which are cost-effective and readily available, manufacturers can effectively reduce CNC machining costs. It’s important to strike a balance between material cost and desired properties to achieve optimal project costs.
Machining Speed and Ease
The machining speed and ease of a material impact both production time and cost. Materials that are more difficult to machine, such as those with lower machinability ratings, require specialized tooling and result in longer machining times. This drives up production costs. In contrast, materials like low carbon steel and aluminum are known for their faster and easier machining capabilities, making them ideal for cost-effective CNC machining projects.
Optimizing Material Selection
To optimize material selection for cost-effective CNC machining, it’s important to consider various factors — from material strength and machinability to cost and availability. By choosing materials like aluminum and low carbon steel that offer a balance between cost, machinability, and performance, manufacturers can reduce project costs without compromising on quality.
Materials | Strength | Machinability | Cost | Availability |
---|---|---|---|---|
Aluminum | Lightweight with good strength properties | Easy to machine; high machinability | Cost-effective | Readily available |
Low Carbon Steel | Good strength and toughness | Easy to machine; high machinability | Affordable | Widely available |
Exotic Metals | Exceptional strength properties | Can be more challenging to machine | Expensive | Availability may vary |
Plastics | Varying strength properties | Can be easily machined | Affordable | Widely available |
Choosing the right material for CNC machining is vital for achieving cost-effective manufacturing. By considering factors such as material strength, machinability, cost, and availability, manufacturers can strike a balance between project costs and desired outcomes. Optimal material selection can help drive efficiency, quality, and overall cost-effectiveness in CNC machining projects.
Cost-Effective Design Approaches for CNC Machining
At Precision Machining Pro, we understand the importance of cost-effective design approaches in CNC machining. By implementing these strategies, manufacturers can minimize expenses while ensuring high-quality results. Here are some key approaches to consider:
Utilize Standard Sizes
One effective way to reduce CNC machining costs is to avoid customization and utilize standard sizes for tooling, raw material blanks, and components. By using readily available resources, manufacturers can save on customization costs and take advantage of economies of scale.
Design for Manufacturing
Designing parts with manufacturing in mind is crucial for cost-effective CNC machining. By identifying potential challenges early on and optimizing the part design, manufacturers can reduce costs. Considerations such as deep pockets, sharp internal corners, and narrow regions can impact machining processes, tool selection, and part quality. Addressing these design considerations early in the process can lead to more efficient and cost-effective CNC machining.
Minimize Customization
Custom elements in part design can increase costs, as they often require additional time and resources for fabrication. Whenever possible, it’s beneficial to minimize customization and utilize standardized components to keep costs in check.
Optimize Tolerances
Tolerances directly impact CNC machining costs. By optimizing tolerance requirements, manufacturers can strike a balance between precision and cost. Assessing the part’s functionality and considering the manufacturing process can help determine appropriate tolerances that achieve the desired quality without unnecessarily increasing expenses.
Enhance Tooling Efficiency
Efficient tooling is essential for cost-effective CNC machining. Choosing the right tools for specific tasks, optimizing toolpaths, and minimizing tool changes can help reduce production costs. By enhancing tooling efficiency, manufacturers can improve productivity and minimize material waste.
Implementing these cost-effective design approaches can lead to significant savings in CNC machining projects. By optimizing design, standardizing components, and minimizing customization, manufacturers can ensure efficient and cost-effective production processes.
Illustration showcasing cost-effective design approaches for CNC machining
Balancing Tolerances and Cost-Effective Manufacturing
In CNC machining, finding the balance between tolerances and cost-effective manufacturing is crucial. By determining the appropriate tolerance requirements, we can achieve precise and reliable parts without unnecessarily increasing production costs. Tight tolerances are desirable for maximum precision, but they can slow down the manufacturing pace and increase the time required for inspection and testing.
Tight Tolerances and Manufacturing Pace: While tight tolerances ensure high accuracy, they may require additional time and effort to achieve. These tolerances often necessitate meticulous machining and intricate processes, resulting in a slower manufacturing pace. Consequently, this may extend the lead time for the production of parts, impacting overall project timelines.
Inspection and Testing: Tighter tolerances also demand more rigorous inspection and testing processes to ensure compliance. The advanced measurement equipment and thorough inspection required for tighter tolerances can increase production costs. It is essential to strike a balance between precision and inspection complexity to minimize expenses while guaranteeing part quality.
Design for Manufacturability: Designing for manufacturability is the key to achieving both tight tolerances and cost-effectiveness. By considering standardization and incorporating design features that enable easier production processes, we can ensure tolerance compatibility and reduce costs. Design considerations, such as feature consolidation or the elimination of complex geometries, can contribute to efficient manufacturing without compromising quality.
Standardization: Emphasizing standardization is another effective way to strike the balance between tolerances and cost-effective manufacturing. By using standardized components and processes, we can streamline production and maximize efficiency. Standardization minimizes the need for custom tooling or extra machining operations, reducing both time and cost.
Comparing Tolerance Levels and Manufacturing Costs
Tolerance Level | Production Costs |
---|---|
Tight Tolerances | Higher production costs due to increased complexity, meticulous machining, and extended inspection time. |
Standard Tolerances | Lower production costs due to simpler machining processes, reduced inspection requirements, and shorter lead times. |
In conclusion, finding the optimal balance between tight tolerances and cost-effective manufacturing is essential. By assessing tolerance requirements, considering manufacturing pace, inspection complexity, and design for manufacturability, we can achieve high-quality parts while minimizing expenses. Striking this balance ensures precision without compromising profitability in CNC machining projects.
Conclusion
In conclusion, CNC tolerances have a significant impact on manufacturing prices. Opting for tighter tolerances generally increases production costs due to factors such as increased scrap, specialized tools, additional testing and inspection, and extra machining processes. However, it is crucial to carefully consider the tolerance requirements to strike a balance between precision and cost-effectiveness.
By implementing optimization strategies, manufacturers can achieve efficient and cost-effective production processes. Key strategies include carefully choosing cost-effective materials, utilizing cost-saving design approaches, and balancing precision, quality, and affordability. Thorough analysis of tooling, inspection methods, material selection, and design considerations is essential to minimize the cost implications of CNC tolerances.
At Precision Machining Pro, we understand the importance of balancing CNC tolerances and manufacturing costs. With our expertise in CNC machining, we offer tailored solutions that optimize costs without compromising on quality or precision. By working closely with our clients, we ensure that their projects are delivered on time, within budget, and meet the required tolerances. Contact us today to discuss your CNC machining needs and let us help you achieve cost-effective manufacturing outcomes.
FAQ
Can CNC tolerances affect prices?
Yes, CNC tolerances have a significant impact on manufacturing prices. Tighter tolerances typically result in higher production costs.
How do tolerance levels impact production costs?
Tighter tolerance levels often lead to increased machining turnaround time, specialized tooling, expensive tests, and additional processes, which can drive up production costs.
How does tolerance influence the manufacturing process?
Tolerance requirements can influence the choice of manufacturing processes, lead times, additional machining operations, and surface finish, all of which can affect production costs.
How do material considerations play a role in tolerances?
Different materials have varying qualities that impact their compatibility with specific tolerance requirements, which can influence manufacturing costs.
What design factors impact tolerances?
Part geometry, overall dimensions, and wall thickness can impact the achievable tolerances, affecting part quality and potentially increasing expenses.
What is the impact of tolerances on parts inspection?
Tighter tolerances require more advanced measurement equipment and inspection techniques, increasing inspection costs and potentially contributing to higher production costs.
How can CNC tolerances be optimized for cost-effectiveness?
Strategies for cost optimization include considering material costs, part complexity, post-processing requirements, CNC machine setups, fixturing, specialized tools, and optimized toolpaths.
What is the significance of material selection in cost-effective CNC machining?
The choice of material can greatly impact project costs, with factors such as material strength, machinability, and cost playing a role in achieving cost-effective CNC machining.
How can design approaches contribute to cost-effective CNC machining?
Cost-effective design approaches involve avoiding customization, utilizing standard sizes, and designing for manufacturability to reduce fabrication costs and optimize CNC machining.
How can tolerances be balanced with cost-effective manufacturing?
Finding the optimal balance between tolerances and cost-effective manufacturing involves considering tolerance requirements, design for manufacturability, and standardization to achieve high-quality parts while minimizing expenses.
Source Links
- https://waykenrm.com/blogs/how-tighter-cnc-part-tolerances-affect-design-and-production/
- https://sybridge.com/how-cnc-setups-affect-project-costs/
- https://www.kellertechnology.com/blog/how-dimensional-tolerances-impact-part-production-costs/